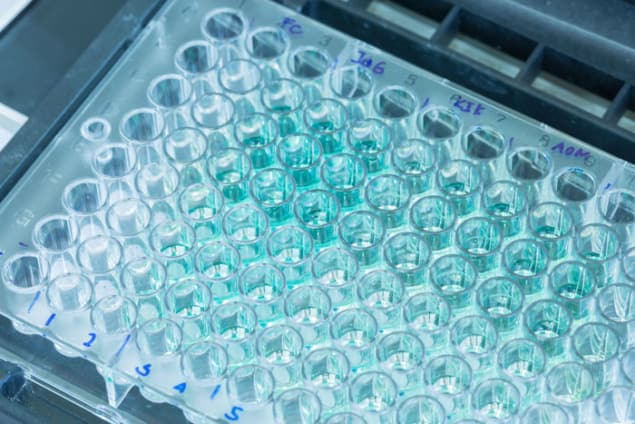
The burden of meeting the food and healthcare requirements for a growing and ageing world population lies on the shoulders of the pharmaceuticals and agribusiness industries. A recent review in Biofabrication highlights the substantial cost of chemical development in agribusiness, pharmaceuticals and even consumer goods, and how this can be minimized by utilizing cutting-edge technology from various fields (Biofabrication 9 033001).
The authors point out that much of the cost of chemical development stems from the need to pass rigorous safety tests before a candidate compound is labelled as safe for consumers and the environment. At the moment this relies on animal research to predict the effect on humans. But while animal research has been the gold standard for many years, its cost and relevancy has now started to be challenged.
Despite researchers’ best efforts, the models used in animal testing are never entirely indicative of potential human toxicity, and high attrition rates in drug development is partly caused by improper translation from animal research to the clinic. The review, authored by members of various chemical development industries, academic researchers, and the NC3Rs (an organization focused on the discovery and application of new technologies and approaches to replace, reduce and refine the use of animals for scientific purposes), gives several examples where recent advancements in biofabrication and bioprinting may provide suitable tissue-engineered models to replace animal use.
The number of alternatives is booming
As an example, liver toxicity is a common benchmark to assess the suitability of novel agricultural chemicals before they are introduced to the market. In vitro models are inadequate due to their simplicity, which to date has dictated the use of animal research. Instead, laboratory tests based on bioengineered human tissue could provide a stepping-stone in the development process, improving the reliability of in vitro tests and reducing the need for animal research.
Likewise, drug development for respiratory diseases such as asthma is hampered by high attrition rates. In this case many new drugs fail at the clinical trial stage, even though they proved effective in prior in vitro or animal studies, since current in vitro disease models fail to reproduce the complexity of the respiratory system. New technologies such as bioprinting could enable these intricate tissues to be manufactured in the laboratory, which may prove an invaluable tool for drug development.
The authors note that consumer goods is another industry sector that may benefit from collaboration with bioengineers. As of 2013, European Union law has forbidden the sales of products that have been tested on animals, which leaves cosmetics and personal care manufacturers with limited means of testing new products. One of the most active fields in bioengineering today is the production of biomimetic and relevant human skin tissue , and these techniques offer promising alternatives to over-simple in vitro skin models and animal research.
Collaboration will be key
Biofabrication has exploded as a very dynamic field over the past 20 years and will soon produce many technologies for industry to exploit and improve product development. As the review suggests, opening channels of communications between bioengineers and chemical developers will be key to stepping further away from animal research.