
A team led by physicists at the University of Nottingham, UK has created a 3D-printed magneto-optical trap (MOT) capable of holding more than 2 × 108 rubidium atoms at temperatures a fraction of a degree above absolute zero. The demonstration shows that 3D printing, which is more formally referred to as additive manufacturing (AM), can meet the demands of highly precise cold-atom experiments, potentially paving the way for portable quantum devices based on this technology.
The starting point for cold-atom experiments is to to trap and cool as many atoms as possible in the smallest possible space. Once this is accomplished, it then becomes feasible to study the atoms’ quantum behaviour, which is only observable at very low temperatures. This behaviour can then be controlled to create some of the most accurate measurement devices in the world, including atomic clocks. A MOT is a key component in this process, bringing together the laser light and magnetic fields that slow the atoms and pin them in place.
Additive manufacturing for optical systems
To construct their 3D-printed MOT, which they describe in PRX Quantum, the Nottingham researchers worked with colleagues at a specialist AM consultancy, Added Scientific Ltd. The process starts with a computer design such as the one shown below. The design is then transformed into a set of instructions that a printer uses to construct a physical object layer-by-layer. The printed components can thus benefit from a mathematically optimized design, making them smaller and lighter than conventionally manufactured components.

The new design incorporates several AM elements, including the mounts that precisely direct laser light into the vacuum chamber containing the atoms (see image). The vacuum chamber itself was built using AM techniques, which further assists in trapping the atoms as it allows careful control of the direction of the magnetic fields that hold the atoms in place. Vacuum chambers built using this technique also have a mass of just 245 g, compared to commercial chambers of up to a kilogram, making them desirable for portable applications beyond the laboratory. They are quick to manufacture, too, meaning that long delivery times for highly specialized designs could become a thing of the past.
As well as making components smaller and lighter, the AM process also introduces new capabilities. The positioning of the laser light, for example, is controlled and regulated via a unit known as the spectroscopy and power distribution apparatus. The adjustment-free AM mounts in this unit enable researchers to insert optical equipment into pre-aligned slots instead of having to fine-tune the setup manually – an advantage that anyone who has spent time in a lab painstakingly aligning optical components will welcome.
One big challenge when constructing optical systems is ensuring that the system is stable and the laser light remains aligned. The new AM design addresses this by reducing the number of times the light gets reflected before it enters the vacuum chamber. With fewer reflections, the beam’s position has less chance of deviating and not reaching the vacuum chamber. Another benefit of the AM approach is that the design contains only enough material to hold the components in place. This reduces the system’s overall weight whilst keeping it cool enough to perform the experiment.
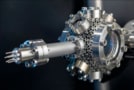
Additive manufacturing makes vacuum systems smaller, lighter and smarter
The inside of the chamber also incorporates advances. Whereas traditional MOT designs generate magnetic fields by running current through coils of wire, using energy continuously, the Nottingham team showed that it is possible to trap atoms with an array of permanent magnets instead. Borrowing a technique widely used in the field of medical physics for MRI machines, they generated the required magnetic field by optimizing the configuration of the magnets.
System performance and outlook
These AM components combine to produce an MOT that can capture 2.5 × 108 rubidium atoms, demonstrating that 3D-printed parts can be successfully integrated into cold atom experiments. “Our approach enables rapid fabrication of complex optical systems while also improving long-term stability,” says team member and Nottingham PhD student Somaya Madkhaly. She adds that AM technology offers even greater scope for miniaturization and improved system performance in the future, with possible strategies that include further optimizing the magnetic field generation to increase trapping capabilities and the automation of the electronic systems.
“3D-printing has become increasingly popular in recent years as it allows direct implementation of intelligent designs and algorithm-based improvements,” Madkhaly says. “In the future, quantum optical installations or vacuum chambers can be used to create new standards using our AM technology.”