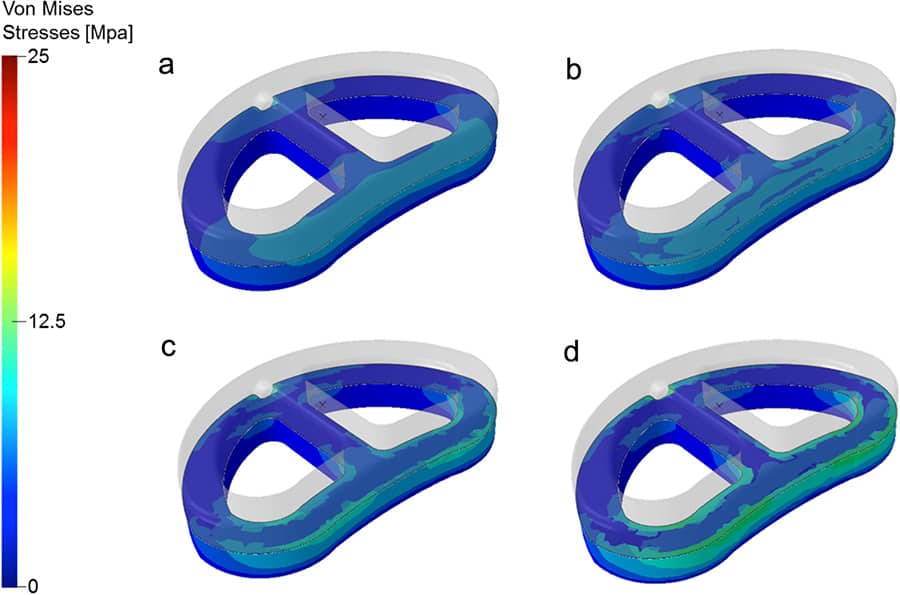
Researchers in the UK recently designed and fabricated anatomically shaped spinal implants using additive manufacturing for the first time. The work, published in the journal Biofabrication, will help in the development of customized implants in the future using data from patients’ own CT and MRI scans.
“The publication of our paper has helped us secure a number of new national and international collaborations,” says team leader Deepak Kalaskar of University College London. “Thanks to these, we are now developing complete custom-made solutions for spinal surgery that combine our current work on spinal implants and newly started studies for developing medical devices and instruments to improve surgical outcomes for complex spinal surgeries – such as those required for treating scoliosis. This work is being funded by Orthopaedic Research UK.”
And that is not all: by closely collaborating with clinicians, Kalaskar and colleagues now have realistic computational models that take into account various patient factors, including the type and severity of their spinal diseases. These models can easily be adopted by hospitals and are a base for further refining implant design using patients’ own pre-operative CT or MRI scans.
There have been several publications in this area from the wider scientific community since the publication of the Biofabrication paper and there is a flurry of interest in the subject across academia and industry. “Our work has been cited by 10 publications within one year of being published, and NewsRX, a US-based tech company, also published an article [in Biotech Weekly] on our research in July 2017 entitled ‘3D printing in spinal surgery’, calling it ‘cutting edge’.”
The researchers say they are now working with an industrial partner to develop custom-built spinal implants. “We have developed computational validation methods and processes to test these implants using individual patient data and will be further validating these via laboratory testing to confirm their translational potential,” says Kalaskar.
Such tests include morphological analysis using scanning electron microscopy, wettability, mechanical evaluation, microstructure analysis using X-ray microcomputed tomography, topographical evaluation at the nanoscale by atomic force microscopy, and measuring the in vitro biological response of the implants.
Coming into its own
Lower back pain is a common affliction in industrialized nations and affects no less than 80% of adults during their lifetime. Severe low back pain is often linked to the degeneration of intervertebral discs and the most widely used surgical procedure to treat this problem, apart from replacing discs completely, is lumbar fusion. Here, surgeons implant an inter-body cage packed with bone graft to promote how bone grows and fuses with the spinal vertebrae.
Most cages available today are made of titanium or polyether ether ketone (PEEK), but neither of these types of device are ideal since they can only be produced in “standard” sizes that are often either too big or too small for individual patients. Anatomically shaped and perfectly matched implants would, of course, be much better since they would fit more neatly and allow bone to heal faster.
Additive manufacturing, or 3D printing as it is more commonly known, is coming into its own here because it can be used to cost-effectively fabricate customized 3D structures with complex geometries. Equally important, those structures can be reproduced perfectly.
In their Biofabrication paper, Kalaskar and colleagues describe how they designed, developed and manufactured anatomical 3D-printed lumbar cages based on a novel composite POSS-PCU – a biomaterial that has already proved itself to be promising for use in a variety of medical device applications.
New directions
The research fits in with the team’s wider research programme, which focuses on developing bespoke implants and devices for musculoskeletal disorders (such as intervertebral disc degeneration and scoliosis) and for repairing and reconstructing various bone defects and providing synthetic replacements for the repair of tendons and ligaments.
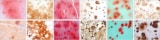
Materials optimization: formulating bioinks for 3D printed constructs
The group is also looking into biofabricating bone and cartilage tissue, which will hopefully help replace diseased or degenerated tissues. The programme brings together the group’s expertise in biomaterials, patient imaging and data analysis, computational modelling and manufacturing technologies.
“While we found 3D printing to be a good technique for printing anatomically shaped implants,” Kalaskar adds, “we are now asking ourselves several questions as regards to reproducibility, scalability and tolerance of additive manufacturing processes. Answering these questions will be essential for clinical translation.”
- This article is one of a series of reports reviewing progress on high-impact research originally published in the IOP Publishing journal Biofabrication.