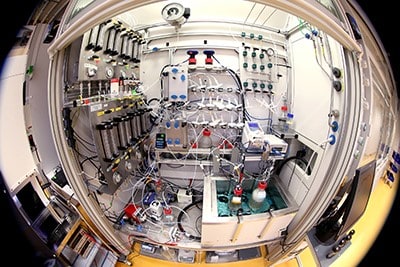
Production of butanol and hexanol may now be environmentally friendly thanks to a process that couples solar-powered electrochemical CO2 reduction and fermentation. Scientists from Siemens, Evonik and Covestro developed the hybrid system, which offers a sustainable, scalable, and efficient way to both reduce CO2 levels and produce value-added chemicals.
Alcohols like butanol and hexanol are widely used in coatings, solvents, cosmetics and fuels. Unfortunately, they are usually produced from depleting fossil sources using a costly and complex process, prompting Guenter Schmid and colleagues to design an alternative.
To drive alcohol production kinetically requires CO. The electrochemical cell in the researcher’s hybrid system uses a porous silver gas-diffusion electrode capable of uniquely high current densities (up to 300 mA cm–2), and an extended lifetime (up to 1200 hours) to produce syngas (CO/H2CO2 from CO2 and H2O, which the bioreactor then converts into valuable alcohols. High current densities are required to drive CO2 reduction at the electrolyser due to the low solubility of CO2 in salt-based electrolytes. The voltage required to drive CO2 reduction is provided by a commercial photovoltaic (PV). This solar cell provided up to 1200 hours of 70% CO-Faradaic efficiency Previously such high efficiencies have only been attained for a few minutes under these conditions or when very high CO2 pressures were used.
Thanks to the high-performance characteristics of the electrochemical cell, the system reached overall photon-to-alcohol efficiencies of 8%, making it one of the most efficient reported for oxygenate production from solar-driven CO2 hydrogenation.
Scaling up: CO2 electroreduction
The researchers also suggest how the process could be scaled up based on the reactions that take place. The cathode reduces CO2 to CO in a reaction that oxidizes water molecules into hydroxide anions (CO2+H2O+2e → CO+2OH–). The water oxidation takes place at the anode, which was composed of an iridium-oxide-coated platinum electrode: H2O-2e → 1/2O2+2H+. The alkaline cathode electrolyte requires an excess of CO2 for its neutralization: full reduction of one CO2 molecule requires three molecules of CO2 (3CO2+H2O+2e → CO+2HCO3-).
Overall, scaling up to produce 10,000 tonnes of hexanol and butanol requires 3.4 × 109 moles of electrons: the CO2 electrolyser provides 16.7% of these electrons, and the H2O electrolyser provides the rest. The plant would consume about 25.5 MW, which 14.6 hectare PV modules would supply. This amount of alcohol would also require 25,000 tonnes of CO2, which amounts to scaling up the CO2 electrolyser by a factor of 270,000, for instance by increasing its surface area of 10 cm2 to 1 m2 (factor 103) and by stacking 270 electrolysis cells.
Scaling up: fermentation
The bioreactor contained two anaerobic cultures, which bioprocessed the alcohols under non-growth conditions: C. autoethanogenum and C. kluyveri. Firstly, C. autoethanogenum transformed CO, H2 and CO2 to acetate and ethanol, which was then further inoculated by C. kluyveri to produce butanol and hexanol.
Scaling the fermentation to produce 10,000 tonnes of alcohols would require an increase in the number of fermenters (bacteria) by a factor of 21.6 × 106. The researchers calculated that increasing the cell concentration by a factor of up to 30 and the volume from 1 litre to 700,000 litres would achieve this. Even though the cultures must be placed in separate containers, these would only require vitamins and minerals for their media.
The hybrid system highlights the importance of research collaboration across diverse scientific fields that can lead to creative and efficient ways to decrease CO2 levels while producing highly desired chemicals. Furthermore, the modular and local alcohol production the research group proposes and the use of renewable energy paves the way to not only eco-friendly but also economically feasible systems for the generation of specialty chemicals.
More information can be found in Nature Catalysis 10.1038/s41929-017-0005-1.