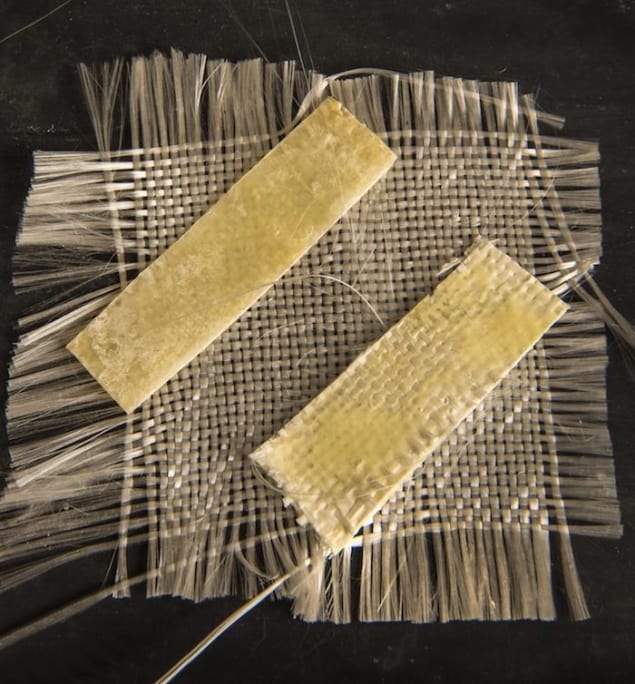
A new recycling process to transform polyethylene terephthalate (PET), which is widely used to make drink bottles and synthetic fibres, can transform the common plastic into a more valuable material with better properties. The new technique could help with the serious and urgent problem of ever-increasing amounts of plastic waste in our oceans and the environment.
With more than 26 million tonnes being produced each year, PET is the most abundantly produced polyester in the world today. Its popularity comes from the fact that it is lightweight, impermeable to water and strong. 60% of this plastic is used in synthetic fibres (for carpets, for example) and 30% in single-use drink bottles. Despite good recycling programmes in many countries, less than 30% of PET bottles are recycled, which means that the material ends up in landfills, where it takes hundreds of years to biodegrade.
Upcycling to fibre-reinforced plastic
“Most PET recycling today is mechanical and results in materials that have a lower value than the virgin plastic so it is actually downcycling,” explains study leader Gregg Beckham of the US Department of Energy’s National Renewable Energy Laboratory (NREL). “Our process takes reclaimed PET and combines it with non-food plant-based building blocks to make materials that are much more valuable (and hence upcycled), have different functions and a longer life than the starting single-use plastic.” Indeed, the fibre-reinforced plastic (FRP) produced could be used in car parts, wind turbine blades, surf- and snow-boards, he says.
The researchers begin by first deconstructing PET (obtained from cut up plastic drink bottles) and glycolyzing it with linear diols (which can be obtained from renewable sources). They then react it with renewably-sourced monomers to produce a series of unsaturated polymers or diacrylic polymers. Finally, they dissolve these polymers in a solution containing reactive free radical molecules to form a resin that they apply to woven fibreglass mat and react to produce a series of rPET-FRPs. The materials produced are as good as, or in some cases even better than, standard composites made from petroleum in terms of both mechanical and thermal properties.
“We hope that this study will motivate other research groups to combine reclaimed low-value plastics with bio-based building blocks and find new strategies for PET and other single-use plastics upcycling,” Beckham tells Physics World. “We need to incentivize the economics of plastics reclamation to keep it out of oceans and landfills.
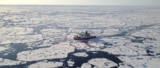
Plastic particles now infest the Arctic
“For our approach in particular, we hope that industry and publicly-funded organizations will come together to further develop this technology.”
The researchers, reporting their work in Joule, say they are now planning to scale up their technique. They also want to find out if they can recycle the composites they have made. “Our reclaimed materials are not inherently recyclable at the end of their useful lifetime so we are working with different formulations and combining them with other bio-based building blocks.”