James McKenzie reflects on the wonders of Gorilla Glass – an invention that protects billions of smartphones, tablets and laptops around the world from unwanted damage
I have a soft spot for accidental discoveries that inadvertently have a profound impact on our lives. Think of the glue that didn’t stick, which was developed by researchers at 3M and led to the ubiquitous Post-it Note. There was Wilhelm Röntgen’s discovery of X-rays, which revolutionized diagnostic medicine. And there was Percy Lebaron Spencer, a physicist at Raytheon in the US, who invented a new type of oven after noticing that microwaves from his radar set melted a chocolate bar in his pocket.
Serendipitous discoveries like these show just why “targeted” product research and development is not always a great idea. The beauty of experiments that are speculative or go wrong is that they can lead to findings you could never predict. Just think about the American chemist Stephanie Kwolek who, in 1964 while working for DuPont, invented Kevlar when her group was searching for a new lightweight yet strong fibre to use for tyres.
But the accidental discovery I want to focus on occurred at Corning Glass Works in upstate New York. Back in the early 1940s, researchers at the company were intrigued by the fact that glass, which is a supposedly transparent material, can darken and change colour if exposed to the heat and light of the Sun for long enough. Keen to investigate this effect, Robert Dalton, a Corning chemist, exposed samples of crystal-clear ruby glass to ultraviolet light and then baked them in an oven. The result: glass with several different shades of colour.
Donald Stookey, another Corning research chemist who had joined the business in 1940, was instructed to explore possible photographic applications of this wonderful new photosensitive glass. His work led to the development of a transparent, aluminosilicate-based glass that became photosensitive if it included trace amounts of gold, silver or copper. Stookey found he could even etch 3D designs into the glass, which was sold as “FotoForm” and later used as a material in electronics packaging and for aperture masks on colour television sets.
The great moment of serendipity occurred one day in 1953 when Stookey wanted to carry out an experiment that involved heating a piece of FotoForm glass to a temperature of 600 °C. The furnace, however, had developed a fault and Stookey mistakenly ended up heating the glass to 900 °C. When he tried to remove the sample from the hot oven, it slipped from his tongs and crashed to the floor. But instead of shattering, the glass – to Stookey’s amazement – bounced.
He had just created the first “glass-ceramic” – a new class of glassy material containing fine crystals of different shapes and sizes dispersed throughout. Subsequent work led Corning to develop this material into the hugely successful CorningWare range of saucepans and cooking pots. Resistant to thermal shock, they don’t break if moved directly from, say, a freezer and into a hot oven. CorningWare became just one of Stookey’s multimillion-dollar inventions.
Donald Stookey: thank him for your iPhone
The Gorilla Glass that protects billions of smartphones and tablets – including all Apple products – would possibly never have existed had it not been for a moment of serendipity by the chemist Stanley Donald Stookey (1915–2014). Working at Corning Glass Works in 1953, his accidental discovery of “glass ceramic” (see main text) led to the development of CorningWare cookery pots, chemically strengthened glass and – eventually – Gorilla Glass itself.
During his 47 years at Corning, Stookey also developed photosensitive glass and Photochromic Ophthalmic glass eyewear, ending up with over 60 patents to his name. In 1986 he was awarded the US National Medal of Technology by President Ronald Reagan. When Stookey retired in 1987 as Corning’s director of fundamental chemical research, his legacy included the Stookey award, which is given each year to a Corning scientist for “outstanding exploratory research accomplishments”.
A unique mix
Trademarked as Pyroceram, the glass Stookey stumbled across had a unique combination of properties, being not just heat resistant, but extremely hard, super strong and transparent to radio waves too. The material also found its way into military applications, being used, for example, in the nose cones of supersonic radar domes in guided missiles. Later, in the 1960s, Corning developed a new kind of Pyroceram material that was not opaque but transparent to visible light.
The company initially chose not to commercialize this newer product, fearing it would cannibalize sales from Corning’s existing and hugely successful Pyrex range of borosilicate glassware, which had been going strong since 1915. But by the 1970s, researchers at Corning France had developed an amber-coloured version of Pyroceram, which they patented and turned into a new range of cookware, going under the Visions brand name.
Meanwhile, as part of an initiative that the company dubbed Project Muscle, Corning had been exploring new ways to make glass stronger. Most glass is strengthened by heating it to a high temperature and then cooling it rapidly so that the outside cools much faster than the inside – a process known as tempering. The temperature gradient puts the inside of the glass in tension and compresses the outer surface, making the glass stronger and less likely to have microscopic cracks and flaws.

As glass gets thinner, however, it becomes ever harder to set up a substantial difference in cooling rate between the core and the surface. In the 1960s researchers at Corning discovered a way of chemically strengthening glass by allowing smaller ions in the glass to be replaced with larger ions from a chemical bath. Thanks to this process of “ion exchange”, the surface of the glass becomes highly compressed, and therefore less prone to the introduction of damage and the application of stresses that could make it break.
Corning sold this glass under the brand name Chemcor and it was used until the early 1990s in various commercial and industrial applications, including car windscreens, planes, drug vials, prison windows, safety glasses and phone booths. Chemcor had varying degrees of commercial success but all that was to change in January 2007 when Steve Jobs, then the chief executive of Apple, took the stage at that year’s MacWorld convention in San Francisco.
Enter Steve Jobs
In front of a whooping audience at the Moscone Center, Jobs introduced a revolutionary new device – the very first Apple iPhone. Until that point, smartphones had been clunky, ugly objects with fiddly keyboards. The new 3.5-inch iPhone promised to transform the market, offering customers a slick, touchscreen device with in-built camera and web-browsing capabilities for the first time.
But the day after revealing the device to an enthusiastic world, Jobs complained that the screen of his own iPhone, which he had been carrying around in his pocket, had ended up covered in tiny nicks. That’s because the prototype iPhone that Jobs had demonstrated was built with a plastic screen, which was mechanically strong but very easy to scratch. A few years earlier Corning had shown Jobs the company’s glass technology and he now insisted that, when the iPhone went on the market just five months later in June 2007, it had to have a glass screen.
Jeff Williams, Apple’s chief operating officer, recalls telling Jobs that his demand was impossible, insisting it would take three or four years to develop glass that was durable enough to meet Jobs’s requirements. “I said, ‘We’ve tested all the current glass and when you drop it, it breaks 100% of the time.’ And he said ‘I don’t know how we’re going to do it, but when it ships in June, it’s gonna be glass’.”
Two days later, Williams got a phone call from Wendell Weeks, Corning’s chief executive. Weeks suggested that Corning’s Chemcor glass, which the company had just started studying again for smartphone use under the name “Gorilla Glass”, could be the solution to Apple’s problem. There followed several months of what Williams calls “sheer terror” as teams at the two companies worked flat out to turn Chemcor into something that would be ready in time for the iPhone’s launch.
The work paid off. “When we launched in June [2007], customers had an iPhone that had the beautiful feel of glass – Corning glass – and was scratch resistant,” Williams recalls. “It helped set the tone for iPhone.” The scratch-resistant glass that shipped on the first-generation iPhone has been a key part of the iPhone success.
Market dominance
In the early smartphones, Corning’s Gorilla Glass was about 1 mm thick – any thicker and the capacitive liquid-crystal displays used at the time wouldn’t have worked well. But despite its thickness, the glass was hard, surprisingly flexible and incredibly scratch resistant, just as Jobs demanded. These days, Corning is on its seventh generation of Gorilla Glass, which is just 0.3–0.5 mm thick. Of course, there are now many competitors who also produce smartphone-glass, including Dragontrail from Japan’s AGC Inc and Xensation from the German firm Schott.
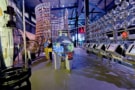
Blown away by the wonders of glass at Corning’s spectacular museum
But Gorilla Glass dominates the market. By 2017 it had been adopted by 40 major manufacturers around the world, being used not only on all Apple iPhones and iPads, but in more than 1800 products from many different firms. According to Expert Market Research, the global smartphone-cover glass market was worth some $1.63bn in 2020, with Gorilla Glass being incorporated into nearly six billion devices. Corning, however, supplies all the glass for Apple smartphones, with the company having used it more and more with each generation of device.
Of course, phones do get dropped and even though Gorilla Glass is incredibly tough, smartphone screens can get damaged. That’s why there is also a healthy market for screen-protection films, which are often made of similar glassy materials. According to a report from MarketWatch this year, the screen-protector market is expected to grow from $2.3bn in 2020 to $5.4bn by 2026. After all, no-one wants to scratch a top-of-the-range nearly un-scratchable smartphone for which they might have paid more than £1000!
Still, can you imagine how the market would have reacted to an Apple iPhone that got scratched every time you put it in your pocket? If Jobs had launched the iPhone with a plastic screen as was originally the plan, I think that could well have killed off the device – however cool the idea was. Jobs was right: it needed to be glass. And to think it can all be traced back to a botched experiment and a faulty oven at Corning Glass Works in 1953. Without that serendipity, we might never be where we are today.