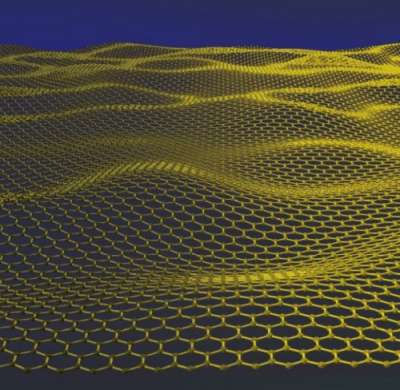
Graphene may be just one atom thick, but the wonder material has yet another application to add to its mounting stack of potential applications. According to the same group of researchers that first fabricated the 2D sheets of carbon nearly four years ago, graphene has the ideal optical properties to form the transparent electrodes in liquid crystal displays (LCDs). The researchers have also developed a technique that overcomes the traditional problems with manufacturing sizable quantities of graphene.
LCDs typically contain an array of many “cells”, each of which consists of a thin layer of liquid crystal sandwiched between a pair of polarizers crossed at 90° to each other. Light entering from behind a cell gets polarized in one direction when it passes through the first polarizer, so when it reaches the second it cannot get through. This makes the cell appear dark. To make the cell bright, the light must pass through the second polarizer, which requires the intervening liquid crystal to rotate the light’s polarization.
To do this, an electric field is applied across the polarizers and this twists the orientation of the long molecules in the liquid crystal. The polarization of the light is guided along the twist of the molecules, and by the time it reaches the second polarizer it has rotated through 90° so that it can pass.
Of course, the electric field has to be applied using electrodes, and these have to be both transparent and good electrical conductors. For such qualities engineers usually turn to indium tin oxide (ITO). However, this material has its drawbacks: indium is rare and therefore expensive; and ITO can release both indium and oxygen ions, which prevent the liquid crystal from aligning correctly. Now, a team including Andre Geim and Kostya Novoselov from the University of Manchester in the UK and Sergey Morozov from the Institute for Microelectronics Technology in Chernogolovka in Russia have found that graphene is generally more transparent than ITO, but with seemingly no drawbacks (arXiv:0803.3031).
Many applications
Graphene comprises a rippled sheet of carbon just one atom thick, rather like a single layer from a crystal of graphite. Indeed, graphene is often fabricated by ripping a layer off a thin piece of graphite with sticky tape, a process known as micromechanical cleavage (or the “Scotch tape method”). Since Geim and colleagues discovered graphene in 2004, researchers have found no end of desirable properties for the material — it can be an excellent electrical and thermal conductor, an equally good semiconductor, and a sensitive mass detector.
A benefit of using graphene for LCD electrodes is that, unlike ITO, it is stable. This prevents it from releasing ions into an “alignment layer”, which is sometimes applied onto LCD electrodes to encourage the liquid-crystal molecules to align properly. Such stray ions can reduce the effectiveness of the alignment layer, causing undesirable “image sticking”. Perhaps more importantly, however, graphene trumps ITO for transparency. Geim’s team used micromechanical cleavage to deposit flakes of graphene onto a glass slide, which they put under an optical microscope. They found that graphene had an optical transmission of about 98%, significantly higher than the 82–85% of standard ITO.
What is doubly impressive about graphene is that it can achieve high optical transmission with a corresponding sheet resistance (a 2D measure of resistivity) of just 6 kΩ. With an added alignment layer of polyvinyl alcohol, which has the side effect of reducing resistance, this figure drops to 400 Ω. Further chemical doping can reduce the sheet resistance to 50 Ω. ITO, on the other hand, has to trade resistance for transparency. Indeed, if an ITO electrode is made thin enough to rival the transparency of graphene, its sheet resistance skyrockets.
Faster production
The one downside with graphene is that, in the past, it has been difficult to produce. Micromechanical cleavage can only produce a few flakes at a time, and is therefore unlikely to ever be employed commercially. However, Geim’s team have developed a new production technique that can reap larger quantities.
They begin by placing crystals of graphite in a bath of dimethylformamide (DMF) and then sonicate it with ultrasound for over three hours. Graphite is hydrophobic which means it tends to clump together in water, but in DMF the sonication allows it to “dissolve” into flakes. Next, the researchers centrifuge the mixture for 10 minutes to remove thick flakes from the monolayer flakes of graphene, which they subsequently spray onto a glass slide. Finally, they anneal the slides for two hours at 250 °C amid hydrogen and argon gas. Although the thickness is not consistent over the slide — it varies between one and four layers of graphene — the optical properties match those of graphene produced by micromechanical cleavage.
Geim’s team are not planning to commercialize graphene electrodes themselves. Novoselov told physicsworld.com that they have had “interest” from the LCD industry, although he could not name the companies to which he was referring. The team will shortly be publishing more fundamental results on graphene’s optical properties.