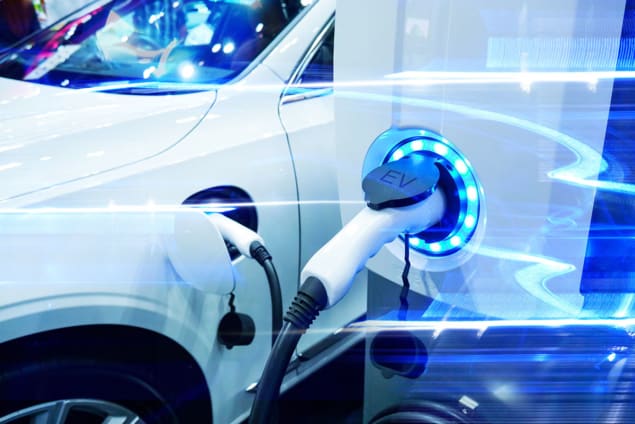
Milk floats were way ahead of their time it turns out. These electric powered carts that trundled from house to house silently delivering milk and dairy at the crack of dawn skipped the whole diesel, petrol-junkie era, leapfrogging from horse power to electric back in the late 1950s. Now consumers are beginning to catch on, opting for electric vehicles for their road trips and commutes in larger and larger numbers, prompting the UK automobile and chemical industries to align their efforts so that vehicle manufacturers can locally source all the required battery components from mined materials to the installed battery pack.
“Over the last few years we’ve been finding out what the size of the opportunity is for the UK for the auto companies and their supply chains,” says David Greenwood, who leads the Advanced Propulsion Systems team at WMG, Warwick University in the UK, and has worked closely with the Advanced Propulsion Centre UK (APC) to inform this latest initiative. “What’s becoming increasingly clear is there’s an upstream opportunity for the chemical supply chain companies to come in and grab up to four or five billion pounds worth of business per year by the mid-2030s if they were to look at producing the chemicals and materials we need for batteries.”
With a projected £4.8 billion per year within the next decade or two on the table, naturally there was a buzz in the air at the launch. The event brought a range of stake holders from both government and industry to the home of the Society for Chemical Industry (SCI) in London. The companies with representatives at the event included international enterprises with significant UK business interests, such as Japan-based Mitsubishi, which numbers the largest electrolyte plant in Europe among its UK assets. Others are currently weighing up the odds for choosing the UK over other European countries for future plants. Sharon Todd, Executive Director of the SCI highlighted the significance of an initiative like this for attracting investment to the UK post-Brexit, as well as some of the challenges, besides the obvious competition with other countries who have already invested heavily in battery technologies.
“If the automotive industry and the chemical industry can come together to accelerate the opportunities through the supply chain – that’s where the UK will see real value added,” Todd told Physics World. This will mean not just sharing investment risks but also synchronizing developments. With the scale and pace of growth expected in the battery industry over the next ten years, timing is key. “There are challenges in that industries and companies haven’t worked this way for some time,” adds Todd. “When SCI was established companies did work like that, that’s how the society was established, but that’s not been the case for many years. So I think there’s a different way of operating across traditional boundaries that will take some time to work through.”
UK assets
As well as the largest electrolyte plant in Europe, the UK has one of the largest supplies of graphite in the world, in addition to healthy reserves of other minerals. Deposits of cobalt – “gold dust in the battery industry” in the words of E4Tech Director Adam Chase – are so abundant they currently exceed resources to process it, so that most of it is exported.
The UK also has a legacy of expertise in battery technology. As APC CEO Ian Constance highlights the discovery and development of the lithium-ion battery, which is expected to power electric vehicles for at least another eight to ten years, is widely accredited to the work of John Goodenough at Oxford University, in the UK. Constance is quick to point out that the work to commercialize these batteries largely took place outside the UK in Japan and that there is plenty of room for improvement for the UK itself to capitalize on “good ideas”.
There are important practical considerations that make a local supply chain particularly desirable for industries using batteries. Shipping batteries and battery components requires hazardous goods protection, and components often require assembling within weeks of being laid out so that losing a fortnight to their shipping can make the manufacturing schedule uncomfortably tight. Batteries are also not just heavy but the most valuable component of electric vehicles – in terms of securing a thriving UK manufacturing industry, if the battery is manufactured elsewhere it may no longer be legitimate to tag the final vehicle as made in the UK.
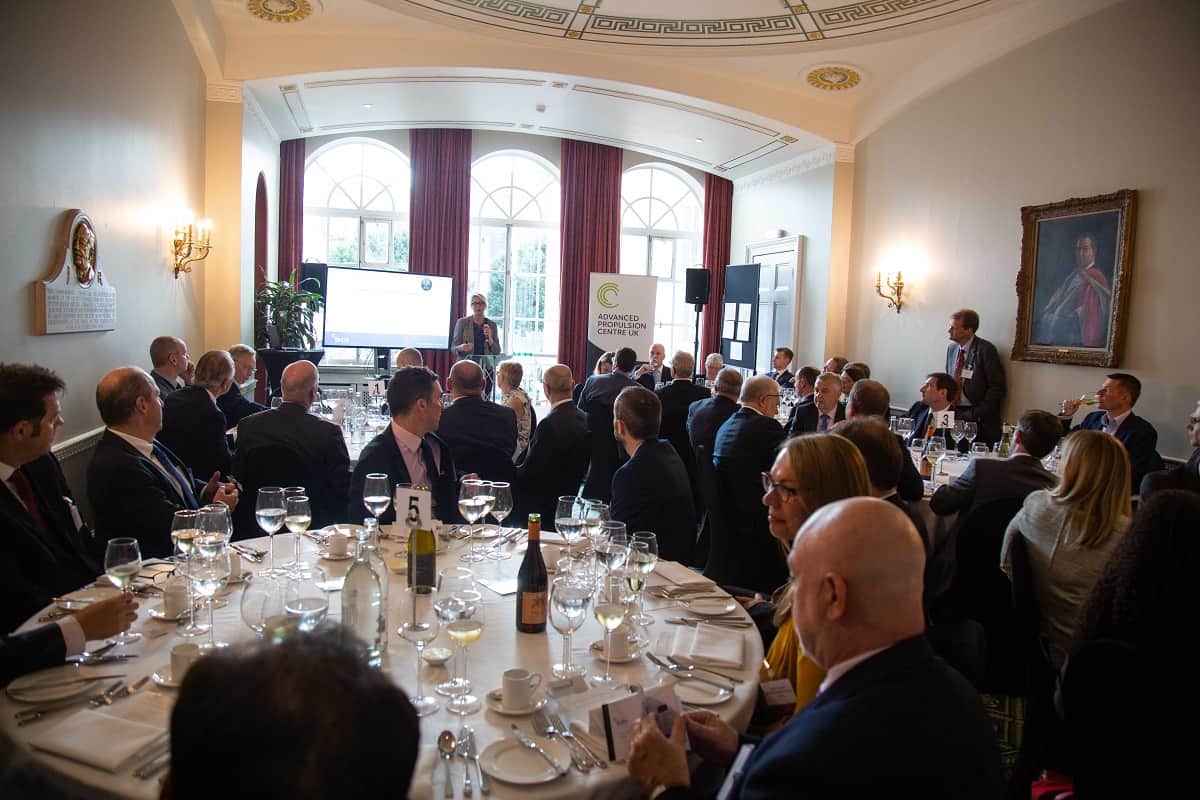
As well as the economics, it is also relevant to consider the environmental impact of globally distributed components for a product that aims to diminish the carbon footprint of transport. Electric vehicles become significantly less environmentally friendly if you charge them with energy from fossil fuels. However as Tony Harper, Industrial Strategy Director for Innovate UK’s Faraday Battery Challenge points out, the UK has a “low and improving carbon grid”. Alongside many other countries renewable energy is on the rise in the UK, so that supporting electric vehicles can genuinely help clean up the air and protect the planet. Constance also expresses interest in the “whole carbon and environmental impact from production through use and recycling end of life”. Here a local supply chain can also play a role. As Todd points out “Local is low carbon.”
All in the timing
While Brexit may heighten interest in a manufacturing initiative with global reach, Constance attributes the motivation to establish a battery supply chain to market demand. “Electric vehicles are taking off,” he told launch attendees over dinner. A lot of people clearly agree as the APC has secured £1 billion funding for projects that bring low-carbon technology to the fore – half from the UK government and the other half from industry. The APC expects to make 25,000 jobs and reduce CO2 by the equivalent of taking 2.4 million cars off the road. UK battery demands for cars and vans alone are expected to reach 70 GW – the output of two Tesla Giga factories.
But the rising interest in electric vehicles is not a reflection of despondent urban motorists in traffic jams finally acknowledging that they never drive faster or further than a milk float anyway. Advances in battery technology means that electric vehicles have a range, durability and performance predictability that increasingly competes with conventional motors. Costs are dropping too so that within the next five to ten years there may be no financial obstacle for motorists with low-carbon, environmentally friendly sympathies wanting to choose electric over petrol. The increasing attraction of electric vehicles is down to improving battery technologies, and there is no sign of deteriorating innovations in this field. So where does this leave industry, with its needs for consistency to return on infrastructure investments?
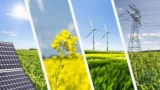
Can crude analysis alone determine prospects for energy materials?
“The really good news is an awful lot of the future technologies we’re talking about are still compatible with the manufacturing processes we use today or if they’re not you only end up replacing 20% of the process and the other 80% is still ok,” says Greenwood. “So it’s not the case that if you make an investment now you regret it forever more. It is an industry that is going to keep moving – you’ll probably see the best battery chemistries moving on every three or four years – but so long as companies are keeping a close eye on that and are preparing themselves for the future, those initial investments won’t be lost there will just be continued upgrades over time.”
The importance of the industry’s agility to keep up with the latest battery technology cannot be overstated. As delegates at the launch confirm, a local supply chain will have numerous advantages, but what will decide where materials and devices are sourced will be the battery performance.