Huub Janssen explains how his firm, Janssen Precision Engineering, has expanded beyond its origins in the semiconductor industry to develop scientific instruments for vacuum, ambient and cryogenic conditions
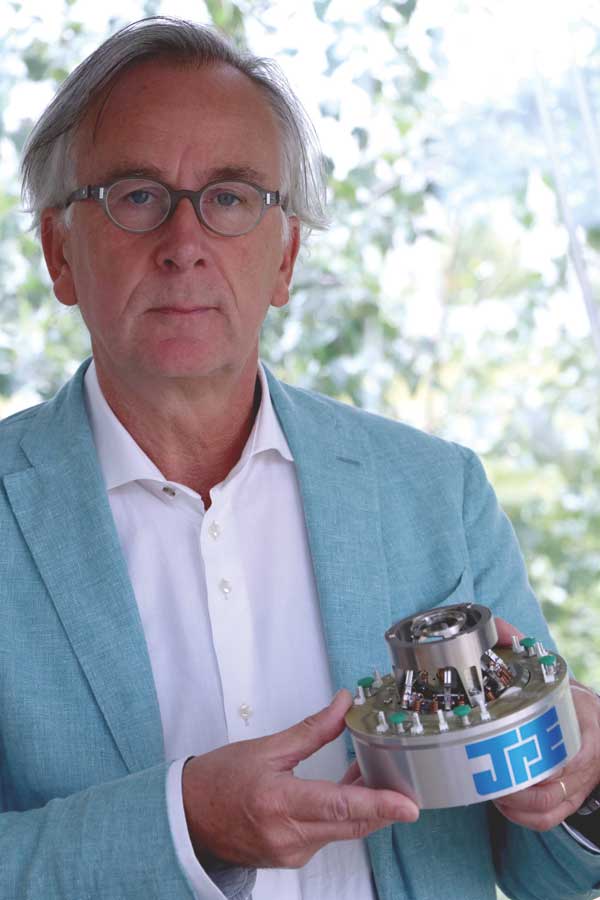
What led you to start Janssen Precision Engineering (JPE)?
I did my degree in mechanical engineering at the Eindhoven University of Technology in the Netherlands, and directly after finishing my studies I worked for a couple of large companies – first for ASML, which makes machines for the fabrication of transistors and silicon wafers, and then for Philips in its liquid-crystal displays business. At Philips, I was responsible for the equipment in two factories, and I did that for about six or seven years, but then a big reorganization within the company meant that the most advanced of the two factories I worked on was going to be closed. This implied that the majority of the interesting work I did would fall away because the other factory was really old-fashioned, so that helped convince me to go for a new challenge. Also, when I was still working for Philips, they asked me to set up projects for external companies, and I thought, “Okay, if I can do this within Philips, I can also do it on my own.”
How did you get funding for the business?
I had some savings, of course, but I didn’t get any external funding, and I also had no orders when I started – I really had to look for customers. However, if you are starting a project-based company there’s not a huge investment involved in finding a desk with a computer where you can do mechanical drawings, and a small space to organize and build mechanical and electronic parts.
How has JPE changed over the years?
Initially, I did project work for semiconductor companies that wanted to move instruments and machines very precisely, in the sub-micron and nanometre range. That was 26 years ago. At that time, I was designing components that could operate in an ambient environment, rather than for vacuum or cryogenics. But maybe 15 or 20 years ago, the semiconductor industry began to shift to a vacuum environment. This was a new challenge, and I like technical challenges. Then, several years later, I got a request from a client in astronomy who wanted a mechanism that would work at cryogenic temperatures, in a liquid-nitrogen environment. We had no experience with those conditions, but we had a brainstorming session, came up with a concept and discussed this with the client. Their reaction was, “Okay, that could work, but we would like to see a proof of concept.” So we built a demonstration unit, proved that it worked at low temperatures, and then went on to develop a complete instrument called a Configurable Slit Unit for the Gran Telescopio Canarias. It’s a kind of diaphragm where you move a mask to block certain stars from the sky, and you can use a computer to change the mask position. It’s a very complex instrument, with lots of actuators and sensors operating in a vacuum and cryogenic environment.
That project took us more than 10 years, with some stops and milestones in-between, and during that time we got a request from scientists who had read that we had experience of positioning objects in cryogenic temperatures. But we had been working at 80 K and they wanted something that would work at 4 K. Well, we never say no! And since then we have been getting more and more requests in that area. A lot of physicists are struggling with instruments in a cryogenic environment – it’s really technologically challenging, so we try to come up with solutions that are at least one step ahead of what people can buy off-the-shelf.
Have you had any significant setbacks? If so, how did you get past them?
As you may know, the semiconductor industry is very cyclical – it has ramped up and ramped down at least three or four times in the past 20 years, and it does it in an extreme way. At times, semiconductor companies will not outsource any work at all, or very little, and then at other times the ramp-up is incredible. You need a lot of flexibility, but you can’t really say to your employees, “Okay, now I need to employ two people, but later I will need 20 or 30.” So I have to find other interesting work, maybe even unpaid work, to give them during the down periods.
Did one of those downturns help lead you into scientific instrumentation?
Yes, I think that’s a good point. You need a mixture. In astronomy, most projects are long-term (sometimes even too long-term, in my view), so the phasing is different from the semiconductor industry.
Any advice for someone thinking of starting their own company in this field?
In this field, I would say that you have to start with a good product, by which I mean you need to make a technological breakthrough in a place where people need it. So I don’t think you should take an instrument that is already on the market and try to improve it, because there is very little chance that you can beat a competitor who already has their product and market organized. But technology breakthroughs alone are not sufficient. They may be enough to get started, but then you have to be aware of the market potential and get it well aligned with your product. Otherwise you will not earn back the money you spent developing it.