Beth Evans is chair of the British Cryogenics Council, which celebrated its 50th anniversary in 2017. Here, she discusses the changing nature of cryogenics and her own work as an equipment developer at STFC’s Rutherford Appleton Laboratory
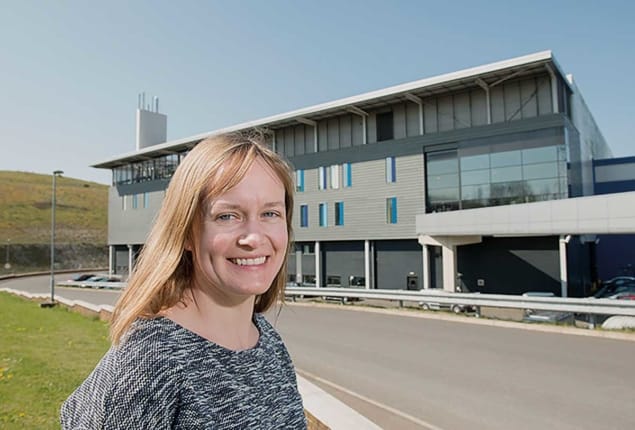
How did you get into cryogenics?
My physics degree at the University of Surrey, UK, included a “sandwich year” placement and one of the places I applied to was CERN. To maximize my chances of getting a job there, I wrote down whole areas that I would be interested in working in, including cryogenics. My interview with the cryogenics group at CERN didn’t go so well (I had actually forgotten what the word “cryogenics” meant), but somehow they offered me the placement anyway, and I loved it. I worked on the Large Hadron Collider magnets, looking at low-conductivity, high-strength materials such as carbon fibre and doing heat-transfer tests at cryogenic temperatures. By the end of the year I was hooked.
What did you do after you finished your undergraduate degree?
I did a PhD at the University of Southampton, UK, researching a type of cryocooler called a pulse tube refrigerator. Most commercial cryocoolers are of the Gifford–McMahon type, which use pistons to expand and contract gases; every time you expand the gas, it cools and you can, in effect, “store” the coolness in a particular area, which you then attach to whatever sample you want to cool down. The pulse tube is different in that it doesn’t have a physical piston moving, just a volume of gas, so there are fewer things that can break and less vibration because you don’t have mechanical things moving at high speeds. Pulse tube refrigerators are now a mature technology – you can buy them off the shelf – but at the time they were still very much in development.
What’s driving the adoption of technologies like that?
The great thing about coolers is that you can switch them on and leave them. You don’t have to continuously refill them with liquid helium and liquid nitrogen – you just press a button and as long as they’ve got electricity and water they keep on going for months, if not years. Another big driver is the cost of helium. Geoscientists have found more helium reserves, but they’re a long way from being brought online. That’s why everybody is turning towards cryogen-free cooling where they can. But liquid helium also has some big advantages. It’s got a lot of cooling power and it’s still relatively cheap to produce, even though the price has been going up. Plus, you need an awful lot of electricity to run cryocoolers. You need electricity to produce liquid helium too, but once it’s cold, it’s cold.
What are you working on now?
I work at ISIS, which is the UK neutron and muon source at the STFC’s Rutherford Appleton Laboratory. Our division provides support for the scientists and users coming to do experiments; we provide the equipment that gets very cold, very hot or reaches very high pressures. One system we’ve designed and built is a low-temperature stress rig – a sort of cold box that you can use to cool your sample, apply mechanical stress to it and then image it with neutrons. It has been used recently to do stress tests on high-temperature superconducting tape, which meant passing a current through the sample while cooling it and applying a tensile load, all while on a neutron beamline. In those circumstances, nothing is simple, not least because when you’re cooling things, they move and contract, and the properties of the material change. For example, many materials that are fine at room temperature become brittle once you cool them down.
Another system we’re working on is a low-temperature sample changer. Most of the time if you want to pull a low-temperature sample out of the neutron beam, you have to warm everything up, put your new sample in and then cool it back down again, which takes quite a long time. We’ve got a sample changer in production that works by attaching the sample to a little parachute, so that we can blow out the sample with helium, catch it with a robot arm, change it, drop in the new sample and let the gas out so that it sails down a tube where the temperature sensor makes an electrical connection at the base. At that point it gets cooled very quickly because it’s a small object and there’s minimal heat transfer. It’s similar to the sample changers used in some types of nuclear magnetic resonance machine. But there are lots of different technologies that have to work together: you’ve got the robots at one end, you’ve got the cryogenics, you’ve got the gas and the vacuum. As is often the case, cryogenics is only one part of a multidisciplinary system.
Aside from uncertainties in liquid-helium supplies, what are the other barriers to progress in cryogenics?
Here in Oxfordshire, we have a lot of cryogenics companies, and our biggest issue is the lack of skilled labour. Cryogenics is a specialized field and until recently you’ve not really been able to study it, either at school or at a technical college. We have helped to change that, and there’s now a university technical college down the road that will be training pupils up in cryogenics and vacuum use. There’s also a BTEC module (that is, a vocational qualification for 16-year-olds) in cryogenics and vacuum technology. We’re trying to make it part of the broader curriculum because cryogenics and vacuum are fundamental to so much of industry and technology. But even so, there’s a shortage of skilled labour. Cryogenics is very dependent on technical skills such as welding – you have to be able to build cryogenic vessels to certain safety standards.
The other issue I’d note is that most cryogenic companies are relatively small, and while they’re very good at what they do, they often don’t have the resources to expand. So if something new comes along, most of them won’t leap up and say “Right, okay, we’ll do that, we’ll develop it” because it’s too much of a risk for them. There’s just not the investment and the infrastructure here in the UK to support some of the big cryogenics projects coming up.
What would help with that?
It would help if there were funds available for riskier projects. Even in academic research, money is given for a specific project, and you cannot fail on that project, so you have to play it safe. And in industry, they can’t do basic development because they have to produce something and sell it – they can’t “play around” because they only get paid for what they deliver. I think that’s probably one thing that’s keeping cryogenic technology and superconductivity technology from growing as it should: industry can’t do development because they haven’t got money for it, and often academics can’t do it either because we’re not really here to develop things – yet if we don’t, industry can’t either. It’s especially hard in this economic climate, where there isn’t any spare money. Government officials like to put money in and get something out, just like in industry, but it’s quite hard when you’re developing technology because you don’t necessarily get the results as quickly as expected.
The British Cryogenics Council recently celebrated its 50th birthday. How has the field changed since it was founded?
Fifty years ago, the cryogenics industry was in its infancy. That’s not to say it was all about fundamental research, but superconductivity was still relatively new; the techniques of making superconductors work in practice were in the early stages; and cryogenics was very academically based. I think that’s been the biggest change. Cryogenics is an enabling technology now rather than a research area. Scientists are still using cryogenics because you can look at atoms and molecules more easily if you slow them down, but it’s also become an industrial tool, used in factories and MRI scanners as well as in particle accelerators.
What do you see as the major trends in cryogenics for the next 10 years?
There’s still a lot of development to be done on superconductivity, especially with high-temperature superconductors. At the moment, a lot of high-temperature superconducting materials are difficult to work with – you can’t roll them out into nice tapes like you can with low-temperature superconductors – so there’s more research needed to help them reach their potential. There are also some interesting “green” applications of cryogenics that may become more important. The so-called “hydrogen economy” has the potential to be huge for the cryogenics industry. If you’re going to run vehicles off hydrogen instead of fossil fuels, you’ll need a lot of hydrogen, and you’ll need to transport and store it somewhere either as a high-pressure gas or as a liquid, bearing in mind that hydrogen reacts with many metals causing embrittlement with long-term exposure. Then there’s the question of how you get the hydrogen into vehicles. If you have liquid-hydrogen filling stations, you’ll have to move liquid hydrogen from an underground tank up and into the vehicle while keeping it at a low temperature. All of that will involve cryogenic technology.