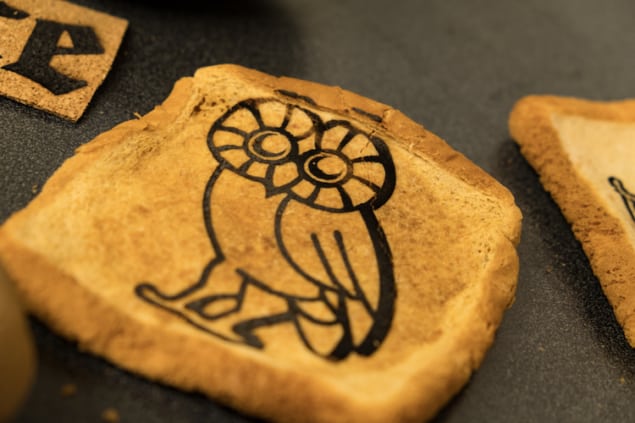
Graphene (a sheet of carbon just one atom thick) can be produced on a wide variety of substrates and even materials such as food, cloth and paper, using a simple multi-pass laser technique. Potential applications include flexible, wearable and even “edible electronics”.
A team led by James Tour of Rice University in the US recently developed a way to transform the top layer of a polymer film (polyimide) into 3D graphene foam using a laser beam. This laser-induced graphene (LIG) consists of microscopic, cross-linked flakes of graphene and can be used to make electronic devices, such as supercapacitors, electrocatalysts for fuel cells, radio-frequency identification (RFID) antennas and biosensors, to name a few.
The researchers have now applied their technique to a wide variety of carbon precursors, including polymers, cardboard, cork, cloth and even certain foods, such as toast, coconut shells and potato skins. Unlike the earlier method, which only required a single laser beam pass, the new technique needs multiple “defocused” passes. “This is because the first laser shot converts the substrate into amorphous carbon,” explains Tour, “and the subsequent shot or two photothermally converts this carbon into graphene as the material selectively absorbs infrared light (in the 10.6 micron range).”
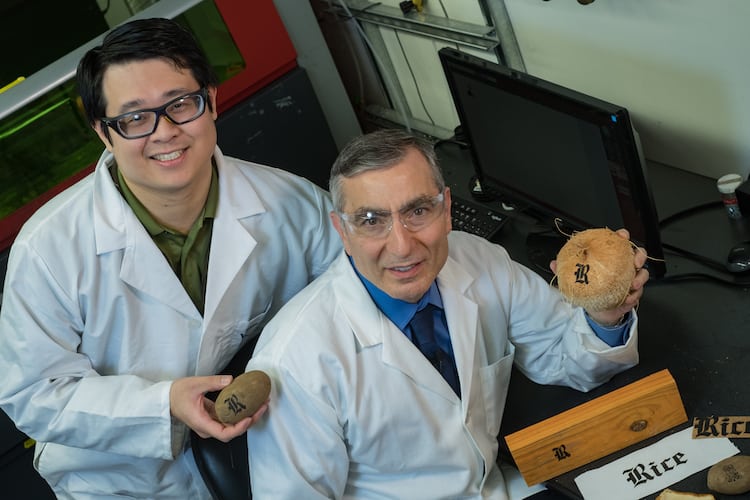
The wavelength of the light is all-important here and the selective absorption of IR light by amorphous carbon is one reason why mere thermal treatments or irradiation with other wavelengths upon carbon precursors do not produce LIG, he adds.
A defocused laser beam is one that is wider and allows each spot on a target to be lased many times in a single raster scan, he explains. “The common denominator in all the wood materials appears to be lignin, a complex organic polymer that forms rigid cell walls. Cork, coconut shells and potato skins have an even higher lignin content (25, 30 and 36% respectively) than oven-dried wood (18-30%), so it is easier to convert them into graphene. What is more, these materials can be processed under ambient conditions.”
As a proof-of-principle, Tour and colleagues fabricated a micro-supercapacitor on a coconut using their multiple lase method. They compared twice-lased coconut with single-lased polyimide processed using the same laser fluence (around 5.5 J/cm2) and found that the coconut-derived material has a higher areal capacitance.
“Being able to produce graphene so easily on such a wide variety of substrates extends our hope for this carbon material,” Tour tells nanotechweb.org. “It means that graphene electronics could be made on a host of different materials and applications such as edible electronics and sensors, and electronics on paper and boxes could see the light of light of day.
“Very often, we don’t see the advantage of something until we make it available,” he adds. “Perhaps all food will one day have a tiny RFID tag that gives you information about where it’s been, how long it’s been stored, its country and city of origin and the path it took to get to your table.
“LIG tags could also be sensors that detect E. coli or other microorganisms on food. They could change colour and give you a signal that you don’t want to eat this. All that could be placed not on a separate tag on the food, but on the food itself.”
The LIG is detailed in ACS Nano DOI: 10.1021/acsnano.7b08539.