To control a plasma at a temperature of 150 million Kelvin, the ITER fusion reactor will need a magnet system like no other, as Daniel Clery explains
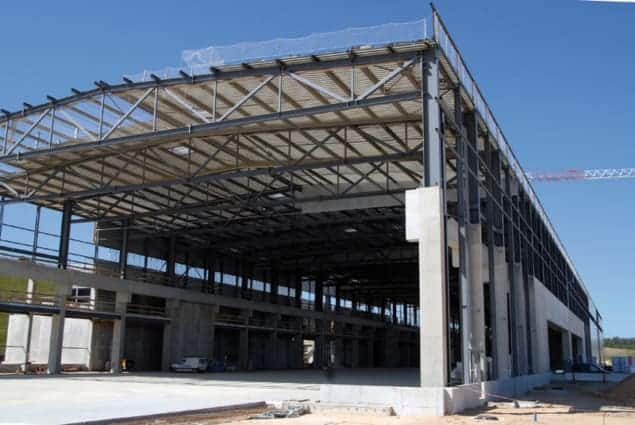
Generating power with nuclear fusion – slamming together hydrogen isotopes until they fuse into helium – has proved much harder to achieve than its nuclear-fission counterpart. But now, after more than 60 years of research, physicists hope they are on the home straight with the €16bn ITER experiment – a huge tokamak now under construction in Cadarache, France. The fruit of a worldwide collaboration involving China, the European Union (EU), India, Japan, South Korea, Russia and the US, ITER is a colossal machine that, once complete in 2019, will weigh as much as an aircraft carrier.
Fusion researchers hope that ITER will be the first tokamak to generate more power than is needed to keep it going – some 500 MW from a 50 MW input. Most of that input heats the fusion fuel – a 50:50 mixture of the hydrogen isotopes deuterium and tritium – to millions of degrees and applies a magnetic straightjacket to hold it in place while it burns. The magnets required to provide that field – 13 T at its strongest point – are now being built in factories across the globe (see table) and are proving to be a huge engineering challenge. They have to endure huge mechanical forces, thousands of current pulses, intense neutron bombardment and a thermal gradient that soars from 4 K to 150 million K across just a few metres. “It’s the scale, not the science, that brings issues,” says Neil Mitchell, head of ITER’s magnet division.
When ITER was being designed back in the late 1980s and early 1990s, it was obvious that the reactor would have to use superconducting magnets because conventional magnets would need gigawatts of power to contain a plasma at a temperature of millions of degrees. A few tokamaks with superconducting magnets had been built before, such as France’s Tore Supra, which began operating in 1988 and stores around 700 MJ of energy in its superconducting magnets. But none have been as big as ITER, which will have magnets that will store a whopping 50 GJ. Indeed, some of the coils are so large that they cannot be transported by road and so will be wound on site at a purpose-built plant.
Magnets in a spin
A tokamak such as ITER has several sets of magnets that perform different roles in confining the superhot plasma within the reactor vessel. The central solenoid is a coil positioned in the central hole of the torus. It acts as the “primary” of a giant transformer with the plasma itself being the “secondary” coil. Driving a current through the central solenoid induces the plasma to flow round the torus, creating a current. This current generates another magnetic field that then “pinches” the plasma current towards the centre and so keeps it away from the walls.
This pinching field is reinforced by “poloidal field” coils – six horizontal, circular coils around the outer edges of the tokamak similar to bands around a barrel. Then there are 18 “toroidal field” coils – huge D-shaped windings that wrap around the plasma. These generate a field parallel to the plasma current that gives it a twist so that the plasma spirals as it moves. This helps to stabilize the plasma and keep it away from the walls. Finally, there are sets of lower-energy “correction” coils that help to shape the plasma.
Despite the challenges of scale, Mitchell says that the magnet technology for ITER is “rather conventional” because it will use well characterized superconducting materials such as niobium tin (Nb3Sn) for the central solenoid and toroidal-field coils, and niobium titanium for the poloidal-field and correction coils. But making an ITER conductor is not just a matter of winding a few strands into a cable. Nb3Sn is a brittle material that must endure enourmous mechanical forces and 60,000 thermal cycles. “It’s very much a challenge,” says Chris Rey, the central-solenoid systems manager at the US ITER Office at the Oak Ridge National Laboratory in Tennessee. “It’s expensive, so you can’t make prototypes. You have to get it right straight out of the box.”
Making the conductor starts with individual strands – each less than a millimetre across – composed of a mixture of niobium and tin that is encased in a copper shell. Three strands are then wound together to make a “triplet”, and 32 triplets are bunched together make a “petal”. Six petals arranged around a central pipe make a cable, roughly 4 cm in diameter, with the pipe allowing the flow of liquid helium to cool the cable to superconducting temperatures. The final part of the process involves encasing the cable in a metal jacket with a roughly square cross-section so that when the conductor is wound into a coil, the windings fit snugly together and cannot move. Prior to the ITER project, around 15 tonnes of this sort of superconducting cable were manufactured per year; ITER requires 400 tonnes – or around 80 km of cable.
To form magnets, the conductors are wound into a metal conduit in the required shape. The largest niobium–tin magnets are the toroidal-field coils that will be arranged vertically around the tokamak. Each one is 14 m tall and weighs 360 tonnes – roughly the mass of a jumbo jet. Once wound, the coils are heated to 650 °C for eight days so that the niobium and tin form the superconductor Nb3Sn.
Testing times
Despite their size, the coils still demand exquisite precision to create a perfect field for plasma confinement. The conductor must be carefully wound into an exact position in the conduit and then held there with an error of only a few millimetres. That sort of manufacturing control is made more difficult by the way that the ITER project is run. Because the seven members of the ITER collaboration all want a share of the industrial contracts, they agreed to divide up the manufacturing between them and each delivers their components to Cadarache “in-kind” without money changing hands. But this means, for example, that making the conductors for the toroidal-field coils has been split between six different member states and, because some of them have contracted more than one company to do the work, a total of 10 firms are involved. “Their grasp of the technology isn’t even,” says Mitchell. “There’s a lot of negotiation and it’s producing a lot of delay. The amount of testing we’re doing is five times what was originally expected.”
That testing threw up a problem earlier this year when a sample of Nb3Sn conductor made in Japan for the central solenoid failed in tests earlier than expected. The specification requires the conductor to survive 60,000 current pulses during the 20-year life of the reactor. However, this particular sample began to fail after only 6000 pulses. “The conductor absolutely works,” says Rey, “it’s the lifetime that’s not understood.” The ITER organization at Cadarache has set up a task force to look into the problem and it will report back later this year.
ITER insiders are playing down the significance of the failed test. It took place at the SULTAN facility at the Paul Scherrer Institute in Villigen, Switzerland, where straight sections of conductor a couple of metres long are subjected to high fields and currents. While this shows that the samples are working, according to Rey it “doesn’t accurately represent the conditions in ITER”. A second sample of the same conductor is now being tested and is reportedly performing much better. An ITER spokesperson says that if the second sample maintains its performance to the end of the test, the conductor is likely to be approved for production next year.
Cost concerns
Another tough decision is whether or not to test the completed coils. In an ideal world, once wound, each magnet would be cooled to 4 K and have high current put through it to see if it worked as expected. Such an approach significantly reduces risk because when the reactor is built, most of the coils cannot be removed for repair or be replaced. But cold-testing such huge magnets – the largest has a diameter of 24 m – also hugely increases cost because it would require a purpose-built facility, much power and a lot of time. There are other risks too: testing one coil in the absence of all of the others might be easier but it would not then experience the full magnetic field of the entire magnet system, and so would have different stresses that could potentially bend it out of shape.
Each ITER member state that is making the magnets must decide for itself whether to do full cold tests on completed coils – and the consensus seems to be that it is not cost-effective. Rey says that the US is planning to test its coils – the six modules of the central solenoid – at a factory in Tallahassee, Florida, by cooling them to 80 K with liquid nitrogen. At that temperature the coil experiences 90% of the thermal stresses that it would encounter at 4 K. Once cool, researchers can test for helium leaks and do a voltage test that stresses the conductors’ insulation. “Most large superconducting magnets fail on their insulation,” Rey says. US ITER managers calculate that it would be cheaper to do the 80 K tests than to ship a faulty module back from France for modification.
But a lack of money will likely persuade project members not to carry out 4 K high-current tests. The US ITER project is still mulling it over – its budget is under severe strain in the current financial climate. The EU, too, is struggling to find its 45% share of the construction cost. In the end, we may not know for sure whether ITER’s magnets work as planned until the day they are switched on at the end of the decade.
- You can download a PDF of the October 2011 Physics World Big-Science Supplement here.