Ultrapure graphene is grown in labs under carefully controlled conditions, but Mark Thompson believes that exploiting the material’s properties on a large scale requires a different approach. Here, he explains how his company, Talga Resources, went from prospecting for gold to developing processes for manufacturing graphene in bulk
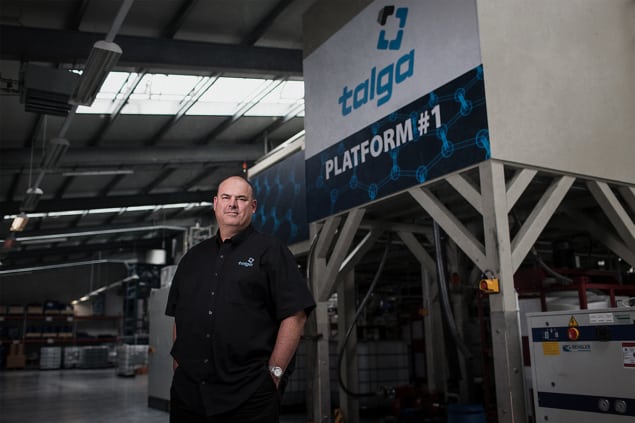
Your scientific background is different from that of most people who work on nanomaterials. How did you get into this field?
Essentially, I’m a prospector: someone who finds things and then brings them to light. I have a lot of experience working on mineral-resource projects, but I’m also self-educated in science, particularly geology and palaeontology. I discovered dinosaur palaeontology when I was in my 30s and on a break from my career in minerals, and I had some success in that field. One of the dinosaurs I helped find was dubbed “the world’s best-preserved dinosaur” by Guinness World Records, and I also discovered one that could be a new species. It’s currently being studied at the Royal Ontario Museum in Canada.
At first, I tried to apply a mineral-exploration approach to palaeontology, bringing modern technology into an old-world business. That didn’t work, but lab-based techniques for investigating fossils have improved massively. We can now sift through the guts of a dinosaur to study its fossilized last meal, look at the pollen and work out the species of plants it was eating 77 million years ago. That sort of clarity wasn’t available before.
Eventually, though, I came back to the world of minerals, created Talga and floated it on the stock market in Australia in 2010. We were planning to look for gold, but we quickly moved towards graphite instead. That became our chief focus in 2011.
Why did you shift away from gold? I mean, for a prospector, gold is sometimes worth thousands of dollars an ounce, whereas graphite…
Gold prices go up and down, usually in cycles. But graphite is used in the anodes of lithium-ion batteries, and the outlook for growth in that market was fantastic. You’re talking about a 25–50% combined annual growth rate, and there’s 10 times more graphite than lithium in a battery. That made graphite a more interesting commodity than gold – at least to us.
What got you interested in graphene?
At a graphite conference in late 2013, I got talking with someone who was working on graphene. He’d been involved with liquid crystal displays (LCDs) from their inception, and he said that for LCD technology, the process from invention to commercialization took about 20 years. I asked, “Well, why be in graphene now, when commercial applications could still be a long way away?” His response was that improvements in computing power mean that we can now model the impact of different materials better, and the way we finance R&D in materials has also matured – with the result that the commercialization process is a lot faster than it was.
That drove me to investigate how we could get graphene from our graphite. The method we now use, electrochemical exfoliation, is usually employed to make graphene from very high-purity synthetic graphite, in the region of 99.9% carbon. But when we tested it on our graphite ore – straight from the ground, costing in the region of hundreds of dollars a tonne to extract – we found to our surprise that we could liberate graphene directly from the rock. With that sort of advantage, we started putting a lot of weight behind scaling up.
Who did you bring in to help you as Talga evolved?
At first we relied on relationships at universities where academics were publishing a lot of papers on these techniques. But very quickly we saw the limitations of this, so beginning in May 2014 we hired chemists and physicists to do our own graphene-processing development and our own graphene product development. We still collaborate with universities, particularly the University of Cambridge in the UK, but predominantly we employ our own team and we now have about 35 people spread across four operations centres.
We’ve followed a vertical integration model. We started with the mineral assets, but to extract the maximum amount of value from them we needed a process that would give us a cost and volume advantage. The next step, bolting on our own R&D, came after we learned that graphene doesn’t like to play well with a lot of materials. It’s probably the world’s ultimate additive (after water), but you have to functionalize it and there’s a lot of chemistry and know-how that goes into making it fit for purpose. That meant we needed an in-house scientific team.
What are the advantages and disadvantages of that model?
The advantages are that in the long term you are almost unbeatable on a cost basis, because you’re not paying a middleman at any stage. You can optimize your production systems to make best use of your natural materials. You do not have the strategic supply-chain problems associated with buying from someone who may go broke or get taken over by another company. And we can keep our intellectual property levels high, because we own everything from the mine up to the customer.
On the downside, our management team is busier. Essentially, we’re developing three businesses instead of one, and each of them has different skillsets. We have a mineral-resource team working in Sweden; our processing team is in Germany; the R&D and product team is in the UK; and the admin and capital comes from our Australian base. That is quite a lot to handle. But we think it is the best way to go and we are very happy with that strategy so far.
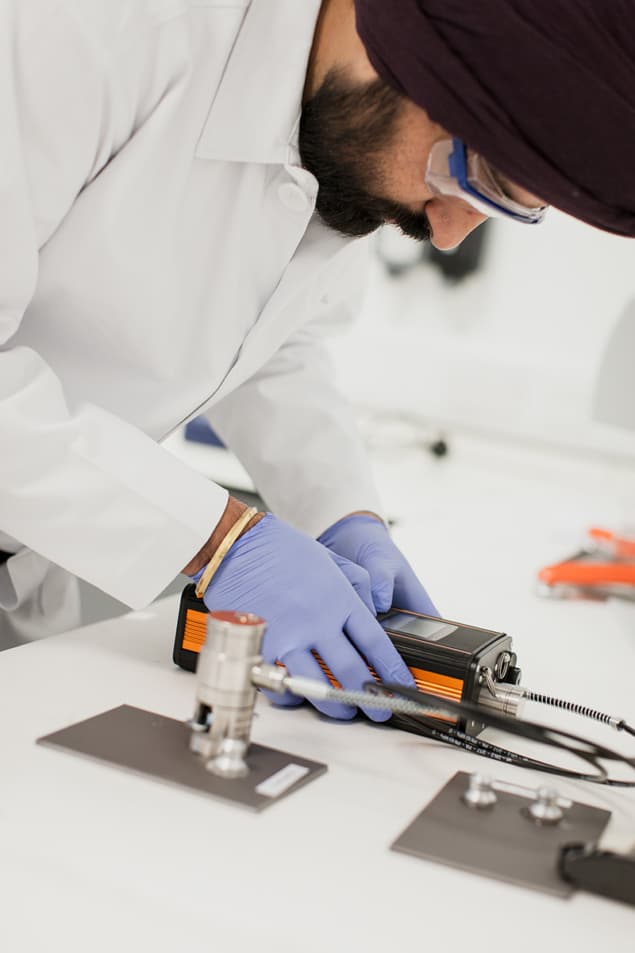
Going back to the graphene-commercialization timeline, we’re now 15 years into the hypothetical 20-year development period. Where do you see the field heading in the next few years?
It’s maturing, but it’s easy to be disappointed by the difference between how fast you think things will happen and how fast they really go. We get weekly cold calls from companies, some with multi-billion-dollar annual revenues, that are looking for a graphene supplier or R&D provider, but the products themselves are still in development. Most companies that buy graphene are using samples to test or develop a product – there’s no really large-scale orders yet.
In the next couple of years, though, I think we’ll see a breakthrough. Some of these test programmes will finish, commercialization decisions will happen, and people will start to need graphene in volume. Eventually, we believe that graphene additives will be a much larger industry, both in value and in tonnage, than the global battery industry is for Talga’s battery products. But the pathway to commercialization is bumpy, and I think that’s why we’re seeing a lot of graphene companies struggling in the capital markets. There will probably be a fair amount of M&A (merger and acquisition) activity in this sector.
Ultimately, though, I think we’re following the same path as carbon nanotubes (CNTs). You had the “valley of despair”, as it were, after a lot of production capacity was built, but today, CNT production is greater than ever. Certainly, the tonnage is far bigger than for graphene, and the prices are still very high. So with the potential for producing graphene at a lower cost than CNTs, and with possibly a much greater range of products, I think the commercialization of graphene is inevitable. It’s just that the focus will be on more basic industrial products rather than the hi-tech stuff that gets all the media attention.
What types of products might create a step change in the market?
I think in the short term it’s going to be coatings, thermal materials and thermoplastics, and maybe also batteries. These products already contain some amount of carbon, and this is where graphene can, I think, be commercialized first – not by creating an entire new class of product or a revolution in performance, but by incremental performance gains from small amounts of additives making a bigger difference and replacing other types of carbon. For example, graphene may replace carbon black in some products and traditional graphite in others. These are maybe not the most exciting applications, but they are certainly very large ones and they will sustain considerable profit margins.
Turning back to Talga, is there anything that you know now that you wish you knew when you started?
That’s a real toughie. I guess maybe I would have moved a little faster to our vertically integrated model. You do get led down a few stray pathways when you’re learning about nano products. Probably, with our own in-house team, we would have learned some of those things a bit faster. But there’s not a heck of a lot I’d change apart from that.
Coming from a mining perspective, we bring a lot of practical efficiencies and scale to what we do. For example, we own the largest natural graphite deposits in Europe, and the Earth’s crust supplied the energy required to crystallize that carbon. We don’t have to do it ourselves. Another way of looking at it is in terms of density. Compared with, say, chemical vapour deposition, where you have to precipitate the carbon out of a gas, we are dealing with rocks that contain up to 50% graphite. You don’t need to move much raw material to produce many, many tonnes of product. We also operate in Sweden, which has super-low power costs and some of the least CO2-emitting power on Earth, so we have a very clean process. And our processing technology is scalable. If, ultimately, someone wanted hundreds of thousands of tonnes of graphene in a pipeline, flowing onto ships somewhere, we could provide that.
We carry this culture into our product development too. We’ve been working for a while on incorporating graphene into concrete, which is seen as a low-value product, but there’s a lot of sustainability and performance benefits in adding graphene to concrete. We didn’t hear much about this before we started talking about it, but there are now other companies interested and university research groups publishing work on it. We feel we helped pollinate that idea because of our large-scale, practical outlook.
Any advice for people working on commercial applications of graphene?
Well, I wouldn’t like to go head to head with us in the future on the production side, so I guess my advice would be to specialize in something. Find a niche. There are many great graphene applications that have been worked on, but haven’t quite made it because, after an initial bout of excitement, there’s not been the right follow-up. Specialize in something where you can follow through and don’t let it go.
- Enjoy the rest of the 2019 Physics World Focus on Nanotechnology & Nanomaterials in our digital magazine or via the Physics World app for any iOS or Android smartphone or tablet.