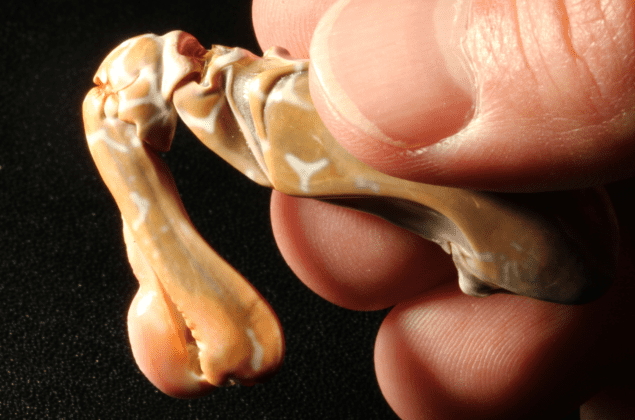
Famous for its great strength, the mantis shrimp pummels its prey with a dactyl club that moves at 80 km/h. But how the brittle material in the club survives repeated high-velocity impacts is something that has puzzled material scientists.
In 2017, theoretical work by US-based researchers showed that the impact energy is dissipated through the twisting of micro-cracks around spiral fibres within the club and that this prevents fibre breakage and catastrophic damage. That work was led by Purdue University’s Pablo Zavattieri and David Kisailus of the University of California, Riverside – and their teams have now performed a combination of computational and experimental studies that back-up this mechanistic theory. Their research also offers a new way of improving the toughness of composite materials.
The aerospace and other industries are keen to develop composite materials that are more resilient and lighter weight than materials available today. Designing better composites is a challenge because there is no ideal tool for predicting the properties of such materials and the slow process of slow trial and error can be the only route to success.
Some scientists are taking a different approach and examining materials that have emerged from nature’s process of trial and error, that is – evolution. In this search, scientists have been drawn to the strength displayed by the mantis shrimp and its smashing dactyl club.
Strengthening fibres
The skeleton of the club is made of calcium carbonate and calcium phosphate – a composition that is expected to be brittle with properties similar to everyday ceramics. However, its strength seems to lie in the spiral- helicoidal architecture of fibres within the club. These fibres are made of chitin, which is a long-chain polymer commonly found in the exoskeletons of crustaceans and insects. In previous studies, composites were designed with a similar spiral architecture. They were found to be much tougher than the traditional quasi-isotropic composite geometry in which the directionality of fibres is shifted by 45° between layers.
It’s okay to have multiple micro-cracks, as long as they don’t coalesce to form one big crack that splits the material
Pablo Zavattieri
Further microscopic analysis of the shrimp’s mighty club revealed that millions of micro-cracks appeared after an assault on a prey. However, these cracks are twisted around the spiral fibres without breaking the fibres themselves. “It’s okay to have multiple micro-cracks, as long as they don’t coalesce to form one big crack that splits the material,” explains Zavattieri.
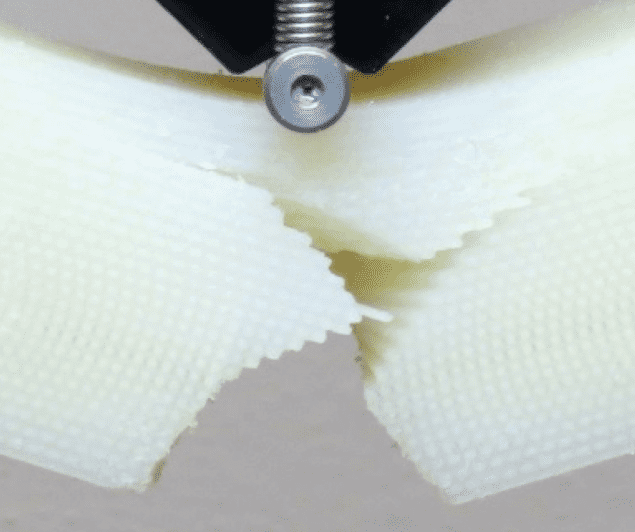
Using these observations, Zavattieri, Kisailus and colleagues delved further into the mechanism of how exactly a helicoidal architecture imparts strength to a material. They proposed the twisting cracks hypothesis – suggesting that the helicoidal architecture enabled the energy from an impact to dissipate within spiral micro-cracks, so preventing catastrophic failure.
To prove this hypothesis the scientists developed a theoretical model backed up by ancillary 3D simulations to examine the local stress intensity factors. This confirmed that as cracks dissipate within the shrimp’s dactyl club, local strain is reduced.
3D printing
The scientists further validated the twisting cracks hypothesis by combining computational and experimental biomimetic models. Composites with spiral architectures were made from carbon fibres and an epoxy matrix using traditional composite processes and 3D printing.
“The advantage of 3D printing is that you can make composites exactly how you want them, with different angles between layers,” says Zavattieri. “Of course there are some differences, because you’re printing fibres 1 mm in diameter and in nature it is a nanometre, but it allows you to demonstrate the mechanism.”
Pressure was applied to the top of the 3D printed composite bars to bend them. In the helicoidal materials the resultant fractures were observed to twist. Camera and digital image correlation techniques were used to examine crack shape, stress distribution and energy dissipation mechanisms. These techniques confirmed the twisting cracks mechanism and demonstrated how it improved fracture resistance in composites.

Secret of super-power shrimp revealed
“They’ve coupled all of the essentials- from examining the microstructure of the natural material to 3D printing experiments- and so clearly demonstrated a successful bottom up design of materials,” says a materials expert, who wished to remain anonymous.
Zavattieri is excited that this basic work can be immediately implemented to create new composites using available technology. He envisions that the extrapolation of these studies will have numerous applications. For instance, Kisailus’ and Zavattieri’s groups are currently developing lightweight fibre-reinforced composites for aerospace, automotive and civil engineering.
“We are beginning to observe that borrowing ideas from nature is very beneficial,” says Zavattieri.
The research is described in the Journal of the Mechanical Behavior of Biomedical Materials and the International Journal of Solids and Structures.