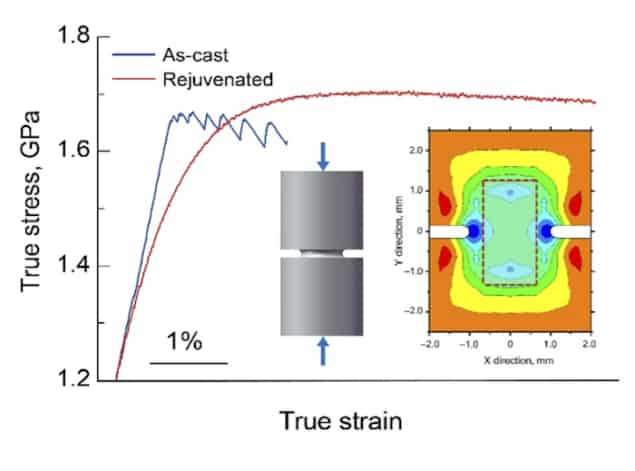
Compressing metallic glasses could make them less prone to fracture, greatly increasing their potential for structural applications. So say researchers from the University of Cambridge in the UK and the Institute of Metal Research in Shenyang, China, who have succeeded in strain-hardening these metastable materials to a degree hitherto thought impossible
Metallic glasses are materials with the properties of both metals and glasses. They contain metallic bonds and are thus conducting, but their atoms are disordered like in a glass, not ordered as in a crystal. They are produced by heating certain substances to above their melting points and then quenching them in a way that prevents them from crystallizing.
While the exceptional strength of metallic glasses makes them promising materials for structural engineering applications, they have one major drawback: they can soften when deformed, which makes them brittle. This contrasts with normal polycrystalline metals and alloys, in which stress produces strain-hardening: under increased loading, plastic deformation in normal metals starts locally, but then spreads uniformly, allowing the material to “stretch”.
Strain softening and shear bands
This ductility, as it is known in metallurgy, is crucial for preventing catastrophic mechanical failure in structures such as steel beams for buildings. Its absence in metallic glasses is thus correspondingly disastrous for structural applications, says project team leader Lindsay Greer of Cambridge. “This is all rather frustrating,” he observes. “Many of the other properties of metallic glasses are highly attractive. For example, they can have a high toughness and show a ‘damage tolerance’ – the product of yield stress and toughness – that is higher than any other known material.”
Greer explains that unlike normal metals, metallic glasses experience non-uniform plastic deformation. At room temperature, deformation occurs via ultra-localized flow in so-called shear bands, leading to instant failure – zero ductility – when the glass is placed under tension. While no similar catastrophe occurs when the material is bent, the shear bands do give rise to unsightly surface markings, which are planes of weakness that evolve into cracks.
Strain-softening and shear bands are the Achilles’ heel of metallic glasses, Greer tells Physics World. Finding a way to strain-harden these materials has thus been a sort of “holy grail” since the earliest days of research on their mechanical properties, he adds.
A rejuvenated metallic glass
Greer and colleagues say they have now found a means of preventing shear banding in metallic glasses during plastic deformation. Their technique consists of compressing cylindrical samples of the glasses in a such a way that the stresses along one axis differ from the stresses in perpendicular directions (see image). This type of compression (known as a triaxial test) causes little plastic deformation, but it does make the central region of the cylinder softer. When the researchers cut out this central region and subjected it to stress and strain, they found that the pre-conditioned, or “rejuvenated”, specimen was much less brittle than the untreated material.
Greer explains that this apparently counter-intuitive result comes about because in the rejuvenated metallic glass, plastic deformation causes the atoms to settle into a denser – that is, atomically better packed – configuration. “This more relaxed state is naturally harder,” he says. “The secret is to simply start with a sufficiently unrelaxed glass that wants to settle/relax in in this way.”
Similar function to annealing
The team confirmed this explanation by using calorimetric tests to measure the energy content of the rejuvenated metallic glass before and after plastic deformation. These tests showed that the energy in the glass does indeed fall during plastic deformation. Thanks to electron diffraction observations, the researchers also calculated that the average interatomic spacing in the material decreases during plastic flow, proving that the atomic packing is denser.
It may seem strange to soften a metallic glass by compression and then study how it hardens upon subsequent plastic deformation, but Greer points out that a similar thing happens when a conventional polycrystalline metallic alloy is annealed, or heat-treated. In both cases, the resulting material is softer, but also tougher.
The major difference is that in a polycrystalline alloy, the annealed state has few defects, making this the low-energy, relaxed state of the system. In this case, plastic deformation generates defects, and the system’s energy increases. In contrast, the rejuvenated metallic glass starts out in a more high-energy state. Its energy then decreases during plastic deformation, producing a glass that exists in a more ordered, relaxed state and has, in effect, a lower defect density.
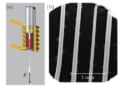
Making metallic glasses more plastic
Wider applications
The new work, which is detailed in Nature, overthrows the idea that metallic glasses can only strain-soften upon plastic deformation, Greer says. The team’s strain-hardening technique is simple and has several practical advantages. For one, it works on metallic glasses of different compositions. It also works for samples that have previously been annealed and made brittle, effectively reversing earlier adverse treatments. Finally, it can be used to create samples of significant size, simply by starting with longer or larger-diameter cylinders.
“We hope that metallic glasses with improved properties could now be made relatively easily and thereby find much wider applications than is currently the case,” Greer says.
Baoan Sun of the Institute of Physics at the Chinese Academy of Sciences in Beijing, who was not involved in this work, agrees. “Finding strain hardening in these metallic glasses will certainly promote their real applications as structural materials,” he says.