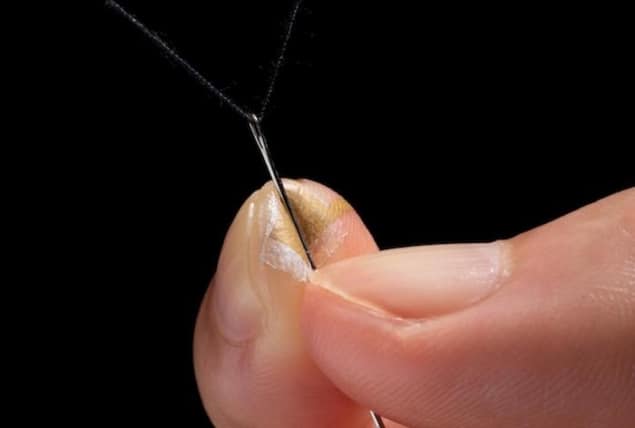
Researchers in Japan have developed the first artificial-skin patch that does not affect the touch sensitivity of the real skin beneath it. The new ultrathin sensor, which is made from multilayers of conductive and dielectric nanomesh structures, could be used in applications as diverse as prosthetics, robot-assisted surgery, human-machine interfaces and wearable health care monitors.
Skin is our largest sensory organ, with an abundance of neurons that continually monitor stimuli in our environment and transmit this information to the brain. A good artificial skin must replicate this ability. In particular, an electronic skin, or e-skin, needs to be highly sensitive to touch, while also responding quickly to applied pressure.
To achieve these goals, the e-skin needs to incorporate a high density of sensors, over areas at least as small as 50 microns. But they also need to avoid interfering with a person’s natural sense of touch, and this has proved difficult. Human fingertips, for example, are so sensitive that a piece of plastic foil just a few microns thick is enough to impair a person’s sensations.
“A wearable sensor for your fingers has to be extremely thin,” explains Sunghoon Lee, a member of Takao Someya’s group at the University of Tokyo and an author of the paper. “But this obviously makes it very fragile and susceptible to damage from rubbing or repeated physical actions.”
For this reason, Lee adds, most e-skins developed to date – made from, for example, sensor arrays of assembled nanowires or microstructure rubber layers that change capacitance or resistance in response to pressure or force – have been relatively thick and bulky.
Two layers
In contrast, the sensor developed by Someya, Lee and colleagues is thin and porous. It consists of two layers, both made using a process called electrospinning, and is based on a design proposed by Akihito Miyamoto and colleagues in 2017. The first layer is an insulating mesh-like network comprising polyurethane fibres around 200 to 400 nm thick. The second is a network of lines that makes up the functional electronic part of the device – a parallel-plate capacitor. This is made of gold on a supporting scaffold of polyvinyl alcohol (PVA), a water-soluble polymer often found in contact lenses. Once this layer has been fabricated, the researchers wash away the PVA to leave only the gold support. The finished pressure sensor is around 13 microns thick.
When a finger covered with this sensor grasps an object, the dielectric nanomesh layer deforms, producing a change in the capacitance measured between the two layers. When the researchers evaluated the device’s sensitivity as determined by the slope of the capacitance change-pressure curve, they found values (of 0.141 kPa-1 in the low applied pressure range of less than 1 kPa and 0.010 kPa-1 in the high applied pressure range of more than 10 kPa) that were comparable to the grip forces measured for a bare finger.
“We performed a rigorous set of tests on our sensors with the help of 18 test subjects,” Lee says. “They confirmed that the sensors were imperceptible and affected neither the ability to grip objects through friction, nor the perceived sensitivity compared to performing the same task without a sensor attached. This is exactly the result we were hoping for.”
Robust and resistant
As an added benefit, the researchers found that their nanomesh sensors continued to work even after being compressed repeatedly. Indeed, the devices’ capacitance changed by just 0.15% after they had been squeezed 1000 times at 19.6 kPa. The conductivity of the gold electrode also remained relatively stable during these experiments.
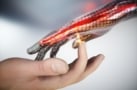
Electronic skin displays human-like reactions to pressure, temperature and pain
Another point in favour of the sensor is its resistance to friction: tests showed that it could be rubbed 300 times with a 50 g object (equivalent to applied pressures of more than 100 kPa) without breaking. The sensor’s electrical characteristics changed only slightly during these tests, and the device remained sensitive to applied pressures even after being rubbed.
The researchers, who report their work in Science, say they plan to increase the number of sensing points in their device and determine how pressure is spatially distributed across it. “We also hope to further develop other imperceptible sensors, such as temperature, strain and humidity sensors, to achieve multimodal sensing,” Lee tells Physics World.