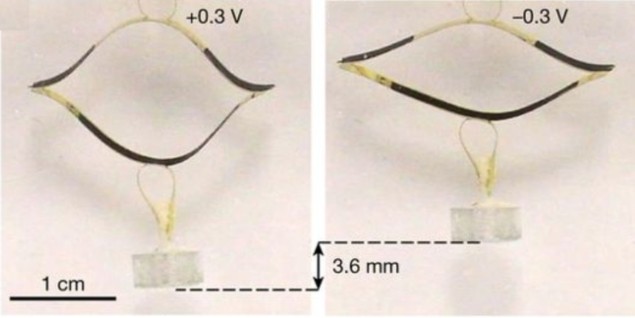
Transforming electricity into movement is a challenge at the root of technologies from robotics to drug delivery, and is performed by a device called an actuator. Researchers in the US have presented an electrochemical actuator made from nanosheets of molybdenum disulphide (MoS2) capable of lifting 150 times its weight consistently over hundreds of cycles. The device can be cycled at up to 1 Hz, which is much faster than the rate achieved until now by similar devices.
MoS2 has a structure similar to that of graphite, with layers of strongly bonded atoms, but weak bonds between the layers. This means it can be exfoliated to form nanosheets, which are then restacked to form thin films with high surface-to-volume ratios. Large amounts of electrochemical charge can be stored in the material as ions by a process known as ion intercalation, which is the same mechanism used in the electrodes of rechargeable batteries. Writing in Nature, Manish Chhowalla and colleagues at Rutgers University describe how the material can harness the movement of these ions to drive an actuator over useful length scales.
Ion intercalation makes movement
The principle underlying the researchers’ device is the mechanical strain exerted from ion intercalation. Positive ions intercalate into MoS2 when it is placed into an appropriate ionic solution. The ions act to pull the negatively charged nanosheets closer together, which makes the material contract in the out-of-plane direction. This results in expansion in a perpendicular plane, causing the structure to become longer and thinner.
The extent of the size change depends on the concentration of intercalated ions, which Chhowalla and his team varied by applying a voltage between the MoS2 film and a reference electrode also in the solution. When the voltage of the film is negative with respect to the solution, more positive ions are intercalated within the material and it lengthens. A positive voltage repels the cations and shortens the film.
To translate this effect into motion, the researchers used a flexible Kapton beam as a substrate for the MoS2 film. By applying a voltage across the system, the change in length induced a strain in the substrate, causing it to bend and serve as an actuator.

So many materials
Actuator performance
Chhowalla and his team found that a voltage that alternated between -0.3 V and 0.3 V was enough to force a useful degree of movement from the plastic beam. The cycle frequency of the driving voltage was varied, and achieved a maximum beam oscillation of around 1 Hz. Although the magnitude of induced curvature begins to reduce at speeds faster than about 0.8 Hz, this is still a much greater rate than that demonstrated by similar devices, which typically operate at only 0.00025 Hz.
The researchers measured the curvature over more than 8000 cycles at 0.2 Hz, and found no signs of degradation. This is a promising indication that the device is robust to both electrochemical and mechanical fatigue. The team also demonstrated that a lifting device using the coated strips was able to lift 150 times its own weight.
The technique that the research team at Rutgers University has presented is clearly an impressive proof of concept. What remains to be seen is how an actuator within an ionic solution can be developed into a useful device, and whether it can be scaled up.