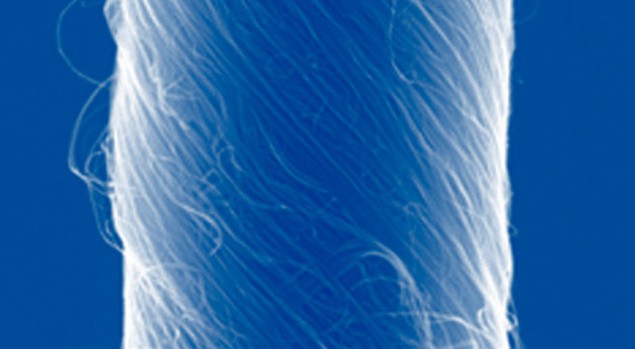
An international team of researchers has invented a new type of artificial muscle that is made from carbon-nanotube threads. The new structures differ from other artificial muscles in that they can twist and turn very quickly.
The new threads could play an important role in technologies that require mechanical movement but where space is limited, says Geoff Spinks from the University of Wollongong in Australia, who was involved in the work. Examples include microfluidics, valves and robotics. The development will be welcomed by nanotechnologists, who have struggled to create nanoscale mechanical actuators. New ideas are required because it can be difficult to build tiny versions of conventional devices – and even when it is possible, such miniature versions often perform poorly.
The muscles, made by a team led by Spinks and Ray Baughman of the University of Texas at Dallas, are composed of thin carbon-nanotube threads, or “yarns”. Carbon nanotubes are themselves hollow cylinders of rolled up carbon sheets, which can be just one atom thick. Key to making the torsional structures is twisting the carbon nanotubes as they are made into a thread, explains Spinks. “The twisting produces a helical structure of intertwined carbon nanotubes,” he says.
Unwinding with a twist
The researchers take lengths of the nanotube thread and partially immerse them in an electrically conducting liquid (or electrolyte). They then hold each end of a thread firmly and connect one end of it to a power supply such as a low-voltage battery. When the power is applied, the thread absorbs some of the liquid and swells. The pressure subsequently produced by the swelling causes the twisted structure to partially unwind, thus creating a rotating action similar to that seen when stretching a helical spring. The structure can be made to rotate in the opposite direction by decreasing the applied voltage.
The team observed the rotation by attaching a plastic paddle to the thread. They found that they could produce rotations of about 250° per millimetre of thread length. This value is roughly 1000 times larger than those observed in previous torsional artificial-muscle systems that are based on ferroelectrics, shape-memory alloys or conducting organic polymers, claims Spinks. And that is not all: the output power per unit mass of the yarn already rivals that of conventional electric motors.
“Carbon nanotubes, which are normally stiff and strong but that have been made more flexible by spinning them into yarns, are ideal for making such muscle-like structures because they have good electrical conductivity,” adds Spinks. “Our work also shows that we can efficiently charge the thread with just a few volts of electricity, and that the threads are strong enough to sustain large weights – for example, the plastic paddle we attached is nearly 2000 times heavier than the thread itself.”
Propelling microrobots
The structures could be useful in applications such as microfluidic pumps, valve drivers and mixers. Indeed, the set-up used by researchers (a plastic paddle attached to the rotating yarns) is a simple mixer in its own right. Mixing fluids on the micro- and nano-scales is difficult but will be crucial for lab-on-chip diagnostics, for example. “Other likely applications are difficult to predict, but we are fascinated by the possibility of using our torsional muscle like a flagellum that would propel a microrobot in the same way it propels a bacterium,” says Spinks.
The team – which also includes scientists from the University of British Columbia in Canada and Hanyang University in Seoul, South Korea – now hopes to study the muscle-like structures in more detail and optimize the yarn geometry. It also hopes to produce even better performing carbon-nanotube torsional muscles by adjusting twist angle and diameter.
The work is reported in Science.