Hiden Analytical’s residual gas analysers (RGAs) are a fixture in big-science laboratories all over the world. So what are the secrets of success in the ultrahigh-vacuum and extreme-high-vacuum regimes?
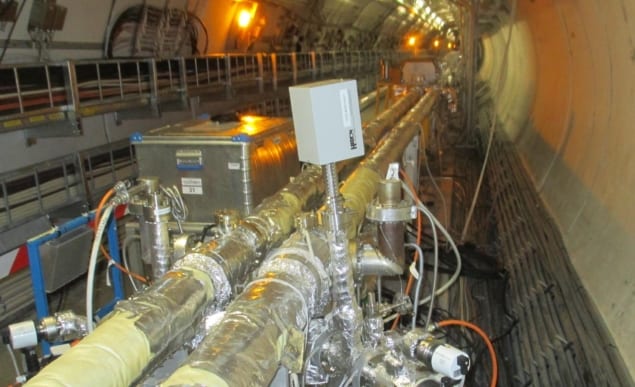
Big science, it seems, is often about the small details – and doubly so when it comes to the ultrahigh-vacuum (UHV) and extreme-high-vacuum (XHV) systems that play a core enabling role in large-scale research facilities such as the Large Hadron Collider (LHC) at CERN, the European Spallation Source (ESS) in Sweden, and the ITER nuclear fusion reactor in France.
Achieving and maintaining UHV/XHV conditions at scale – broadly the pressure regime from 10−7 mbar through 10−12 mbar and lower – is a complex engineering challenge that would simply not be possible without the online, real-time diagnostic capabilities of compact and robust quadrupole mass spectrometers known as residual gas analysers (RGAs).
These workhorse instruments effectively “police” the UHV/XHV environment at a granular level – ensuring safe and reliable operation of large-scale research facilities by monitoring vacuum quality (detecting impurities at the sub-ppm level), providing in-situ leak detection and checking the integrity of vacuum seals and feed-throughs.
Vacuum versatility
One of the leading suppliers of RGAs to the big-science community is UK-based manufacturer Hiden Analytical which, as well as the aforementioned facilities, services a posse of high-profile global customers with its RGA offering – among them Brookhaven National Laboratory (BNL), SpaceX and NASA in the US; the European Space Agency and the European Gravitational Observatory; as well as the Diamond Light Source and the Culham Centre for Fusion Energy (CCFE) in the UK.
“We have RGAs deployed at all these big-science sites and more,” says Peter Hatton, managing director of Hiden. “Our instruments are used not only for routine UHV/XHV monitoring, but also to support the advanced research projects that underpin all large-scale science facilities – whether that’s surface analysis via secondary-ion mass spectrometry, UHV thermally programmed desorption studies or all manner of gas analysis applications.”
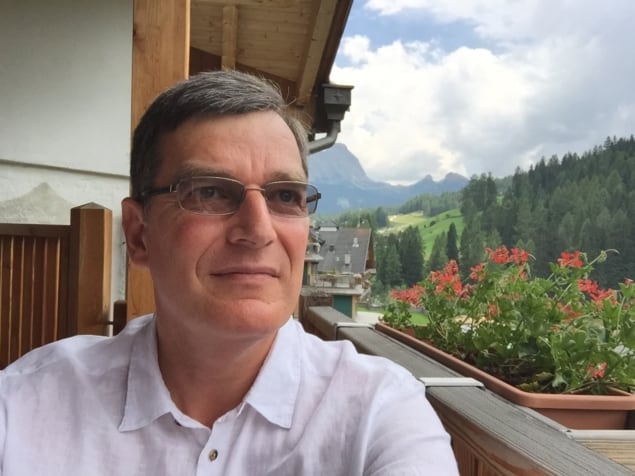
Hiden, for its part, has more than 35 years experience as a supplier of application-specific quadrupole mass spectrometers, including RGAs. As such, the company’s in-house manufacturing model combines state-of-the-art cleaning, metrology and assembly techniques with the firmware and software needed to give its analysers the sensitivity, stability and dynamic range for diverse research and industry applications.
“The collaborative nature of our business is a big differentiator,” Hatton explains. “We listen and learn from all our customers, who gain from having personal support from the engineers directly involved in the development, manufacture and test of their product.”
A case study in this regard is the National Synchrotron Light Source II (NSLS-II) at BNL in Upton, New York. Hiden was selected as a preferred supplier for NSLS-II in 2011 after extensive evaluation of its RGA product line for UHV/XHV applications – specifically the HAL 201 RC, which offers a minimum detectable partial pressure of 5×10−14 mbar. Since then, it’s been a productive relationship in terms of sales and product innovation. For starters, the scale and complexity of projects under way at NSLS-II necessitate a networked vacuum diagnostics capability and, all told, there are now more than 100 Hiden RGAs integrated with the laboratory’s central control systems via EPICS software drivers.
“Supplying projects like NSLS-II also requires full cognisance of some pretty harsh operating environments,” adds Hatton. “With this in mind, we have developed a ‘radiation-hard’ RGA (the HAL 101X) that can operate with no smart electronics within 100 m of the analyser location – a tough ask given that everything is micro-controlled these days.”
Collaboration equals innovation
In Europe, meanwhile, Hiden’s eagerness to learn from its customers is equally prominent – perhaps most notably CERN’s vacuum, surfaces and coatings group. With operational responsibility for the particle physics laboratory’s extensive vacuum infrastructure, this team of more than 60 scientists and engineers also manages a network of 200+ RGAs across the CERN site in Geneva – approximately a quarter of those analysers being supplied by Hiden.
There are three main applications for RGAs at CERN: commissioning of UHV/XHV systems in the laboratory’s particle accelerators and detectors – monitoring of possible contamination or leaks, for example, between experimental runs of the LHC; pass/fail acceptance testing of vacuum components and subsystems – collimators, magnets, pumps and the like – prior to deployment in the accelerators and detectors; and a range of offline R&D activities, including low-temperature UHV/XHV characterization and desorption studies of advanced engineering materials.
“What we appreciate from Hiden is their responsiveness – we always get a quick answer on any after-sales issues regarding hardware or software,” explains Sophie Meunier, senior vacuum engineer with responsibility for RGA technologies at CERN. “They know their products inside out,” she adds, “because they handle all aspects of the manufacturing and software development in-house.”
That forensic product know-how and attention to detail proved to be essential in addressing CERN’s stringent outgassing requirements for its UHV/XHV systems – and in particular the hydrogen outgassing rate of the RGA ion source (which must be less than 1×10−8 mbar·l/s two hours after switch-on). “The outgassing rate of the ion source is a critical success factor in RGAs destined for UHV/XHV applications,” explains Meunier. “In simple terms, we want to measure the partial pressure of our UHV/XHV systems – not the outgassing of the RGA ion source.”
Achieving this figure of merit – and delivering an ion-source solution that meets CERN’s RGA specifications for the long term – was very much a collaborative endeavour between customer and vendor. The joint testing and optimization effort addressed the ion-source components, enhanced source geometries and evaluation of materials compatible with vacuum-firing to 900 °C. All of which ultimately enabled Hiden to implement its own custom manufacturing set-up, pretreating RGAs with specialist cleaning, vacuum-firing and bakeout procedures prior to deployment at CERN.
That customer-centric approach also informs Hiden’s software development. Consider the RGA user interface and data visualization. Meunier and her colleagues at CERN have a requirement for the laboratory’s RGAs to provide a read-out of ion current as the primary measurand (rather than pressure, which requires a conversion factor). “When we asked, Hiden delivered, incorporating our request into the latest version of its RGA software MASsoft Professional,” Meunier notes. What’s more, MASsoft provides additional flexibility for big-science end-users by allowing instrument control via USB 2.0, RS232 or Ethernet data protocols.
Hardware and software innovation notwithstanding, Hiden’s RGAs must also measure up against another unforgiving benchmark – reliability – if they are to enable big-science facilities to minimize vacuum downtime and ultimately reduce their operating costs. “Reliability and longevity are non-negotiable,” Hatton concludes. “That’s why, as well as a three-year warranty, all our products are supported by a lifetime application support guarantee. Worth noting also that we continue to support the first instruments that we manufactured over 35 years ago.”
Small details, it seems, really do go a long way in big science.