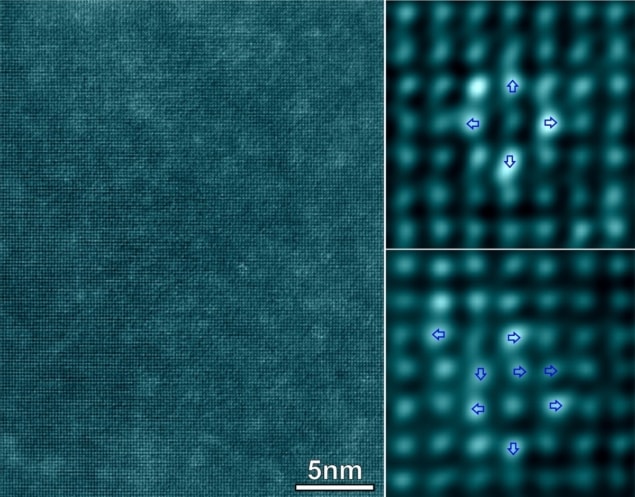
Aluminium alloys are widely used in many industrial applications including automobiles and aeroplanes, on account of their light weight. However, the wide-spread use of such alloys was contingent on the discovery of precipitate strengthening as a means for improving the tensile properties of these alloys necessary for most applications. Discovered over a hundred years ago, the technique involves heating alloys to elevated temperatures, which allows nanoscale secondary phases to precipitate in the metal. These precipitates hinder dislocation motion throughout the material and greatly increase their tensile strength. Now, however, Australian researchers led by Christopher Hutchinson at Monash University have developed a room-temperature cycling technique that reproduces and improves these material properties much more quickly and cheaply.
The inclusion of nanoscale precipitates into high-performance alloys is a key mechanism for improving their tensile properties for many industrial applications. These precipitates are often of a different phase from the bulk alloy and require large energy barriers to nucleate as well as increased diffusion for their formations. Hence, some of the most used aluminium alloys are “baked” for hours at between 120 °C and 200 °C to promote precipitate nucleation and growth. This technique, though in use since 1906, is highly demanding in terms of both time and energy.
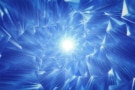
Why gradually does it for maximizing strength
Here, the researchers have developed a novel technique dubbed cyclic strengthening (CS) which, as its name suggests, cyclically stretches and compresses the metal without heating it. This cyclic stress creates vacancies in the materials by dislocation motion, which allows for increased diffusion and hence precipitate formation, leading to improved mechanical properties of the alloys.
From baking to cycling
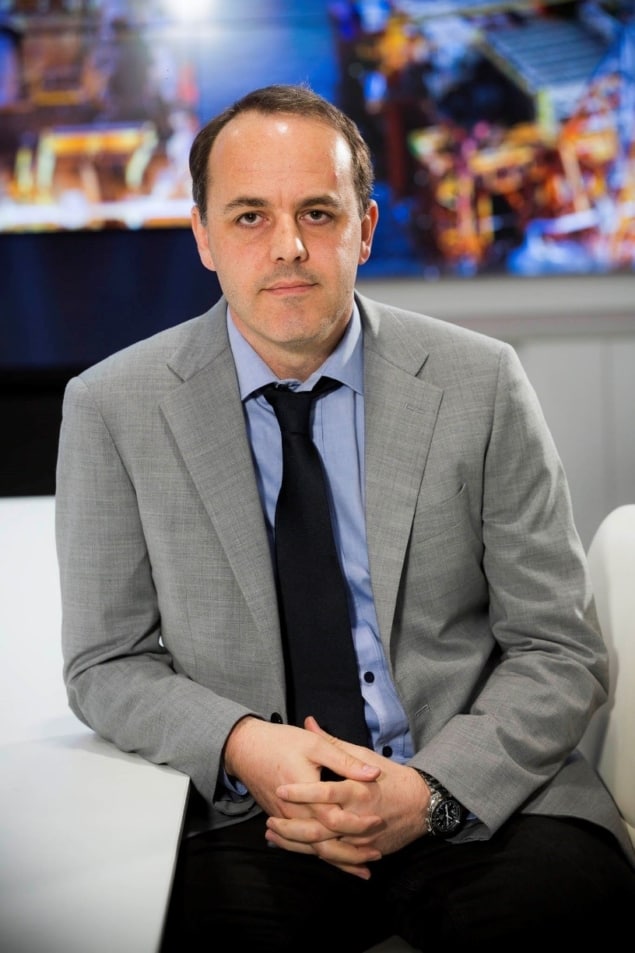
The properties of the aluminium alloys treated by CS give equal or better strengths to heat-treatment but also improved elongation behaviour. This is explained in part due to the different nature of micro-damage sustained by the metals during CS treatment. Indeed, a caveat of thermally aging alloys is the formation of precipitate free zones (PFZs) near grain boundaries. The high diffusion rates at elevated temperatures allow precipitates and vacancies to annihilate at grain boundaries leaving 20–200 nm weak precipitate-free regions near grain boundaries. The CS method, however, does not induce the formation of such zones and instead, homogenously distributes strength throughout the material, which explains in part the improved extension behaviour of the alloys.
The researchers have not yet fully determined the exact nature of the precipitates formed during CS treatment but they are much smaller, on the order of 1 to 2 nm, than those formed during thermal treatment. What is even more notable is that the CS technique is highly rapid allowing for treatments that take only minutes to complete using high cycling frequencies. This new method provides a cheap and extremely quick alternative to traditional precipitate strengthening methods for aluminium alloys overstepping a century-old technique.
Full details of the research are reported in Science.