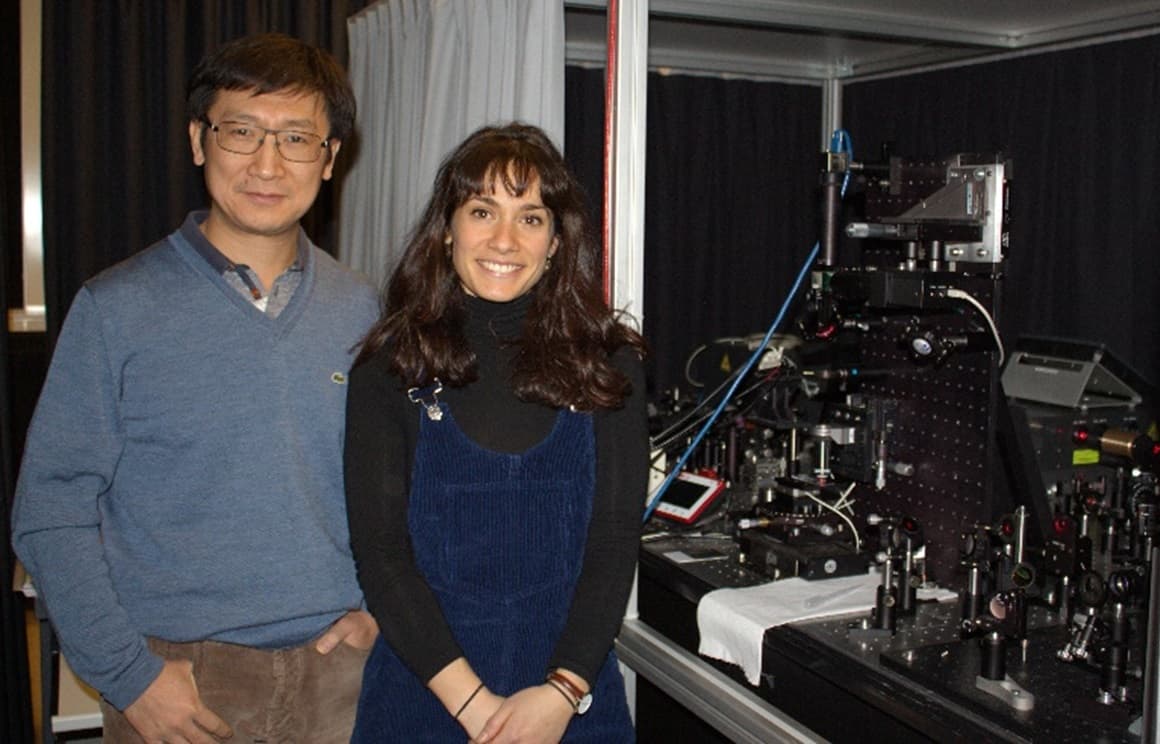
Researchers in Switzerland have employed multiphoton laser direct writing (MP-LDW) to polymerize a monomer called phenylacetylene, which is only sensitive to deep ultraviolet light. They utilized MP-LDW and phenylacetylene to fabricate, for the first time, 1 μm wide light-guiding structures in polydimethylsiloxane (PDMS), in order to make smaller and more complex biomedical devices (Opt. Mater. Express 10.1364/OME.9.000128).
PDMS is an elastomer commonly used to fabricate optofluidic and microfluidic devices. Creation of these flexible light guides (waveguides) has become necessary in the development of biomedical and biosensing platforms, including biosensors, optogenetics, wearable photonics, optical printed circuit boards and microfluidic flow cytometry devices, for example.
Fabricating biomedical devices requires the creation of complex structures inside glass and polymer-based materials, which can be achieved using femtosecond laser micromachining. When passing through a medium, the high-intensity ultrafast laser light results in the simultaneous absorption of multiple photons through a nonlinear process. The combined energy of those photons triggers a molecular transition inside the material, which leads to structural modifications, such as association (photopolymerization) and dissociation (photolysis) of molecules.
Since most monomer molecules can only absorb deep ultraviolet light, photopolymerization usually relies on a photoinitiator to convert the absorbed light energy into chemical energy in order to proceed efficiently. Upon absorption of visible or ultraviolet light, a photoinitiator produces reactive species that transfer the chemical energy to monomer molecules and start a chain-growth polymerization. In biomedical applications, where biocompatibility is of great importance, ensuring that the photoinitiator is nontoxic is crucial. Eliminating the photoinitiator and minimizing the chemical complexity would be even more beneficial.
PDMS waveguide fabrication
In this latest work, the researchers — from the École Polytechnique Fédérale de Lausanne (EPFL), led by Demetri Psaltis — fabricated PDMS optical waveguides for the first time without employing a photoinitiator, by using MP-LDW. Past studies reported 50 µm-wide waveguides with a refractive index change of approximately0.01 and between 0.3 and 0.6 dB/cm optical loss at 850 nm. The EPFL researchers achieved a PDMS waveguide with a core size of 1.3 µm and a high refractive index contrast (0.06 or above) between the waveguide core and the PDMS cladding.
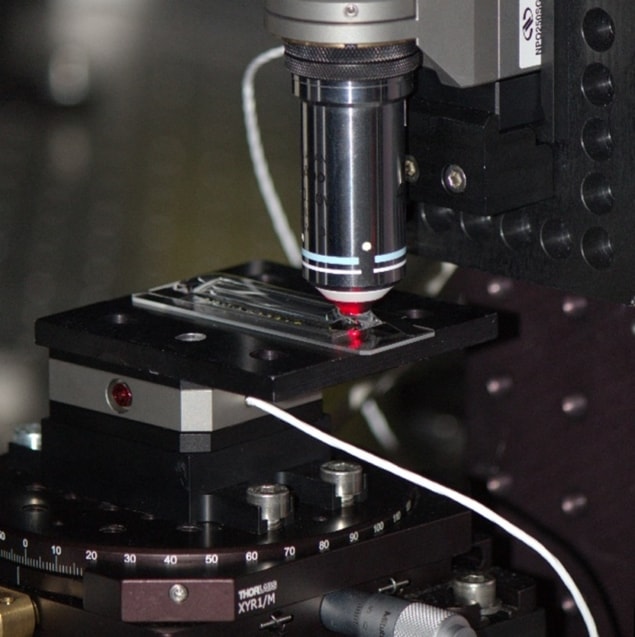
The fabrication was performed with a femtosecond Ti:sapphire laser tuned to 680 nm. The resulting waveguides had a particularly low optical loss of 0.03 dB/cm in the 650-700 nm spectral band. This low light loss allows a light signal to travel efficiently though the waveguides before facing severe signal degradation.
The researchers used phenylacetylene as the monomer, whose absorption band falls in the deep ultraviolet band and is only accessible through multiphoton absorption. The dense -electrons in phenylacetylene molecules helped achieve the high refractive index contrast.
Team member Ye Pu believes that the new waveguides are the smallest ever created in PDMS. “Our flexible waveguides could be integrated into microfluidic lab-on-chip systems to eliminate bulky external optics needed to perform blood tests, for example,” he says.
To advance the device for future possible clinical applications, the researchers are now working to develop a control system to monitor the fabrication process during laser writing. This will also help to avoid material damage.
The researchers also plan to construct a flexible endoscope, which Pu suggests would allow imaging of several hard-to-reach places in the body, requiring only minimally invasive surgery.