The ability of trees to cool by transporting water from their roots to the leaves has been known for centuries. But as Stephen Ornes discovers, the principles of transpiration are also inspiring innovative techniques to cool vehicles travelling at hypersonic speeds, where unwanted heat is a problem too
The tallest known tree in the world is in Redwood National Park, a few hundred kilometres north of San Francisco, just inland from the Pacific coast. You won’t find its location marked on official hiking maps, however. That’s because the two amateur naturalists who discovered the tree in 2006 – Michael Taylor and Chris Atkins – have tried to keep its whereabouts a secret, fearing that tourists and looters might carve a mark or chisel off a chunky souvenir to take home (though you can see its approximate location on unofficial guides). They named the tree Hyperion and the intrepid climbers who measured it – using a laser and a measurement line dropped from the top – reported that this botanical titan rises about 116 m above the forest floor. That makes it a little over 1 m bigger than the second-tallest-known tree, a redwood called Helios.
Hyperion, like all trees, hides in its trunk a remarkable natural engineering process that keeps the plant hydrated and cool. Known as “transpiration”, it involves water entering the roots and travelling up the trunk before passing out via the leaves. It’s an invisible and silent process that lets a single, 90 m-high redwood shuttle about 2000 litres of water from roots to leaves in a single day – that’s more than 400 flushes of a low-volume toilet. Of course, you don’t have to bore into a redwood’s 6 m-wide trunk to find evidence of transpiration; small plants do it, too.
Details about the mechanics of transpiration were first published in 1727 by the English botanist and clergyman Stephen Hales. Water that has entered a tree via its roots flows up through the “xylem” – hardy, tubular cells in the stem that are stacked together to form a natural pipe that reaches all the way up. With thick cell walls that add structural support to the plant, xylem become useful as water carriers once they reach maturity, at which point they’re completely dead. The water then evaporates into the air through tiny pores, or “stomata”, lying on the undersides of the leaves (figure 1).
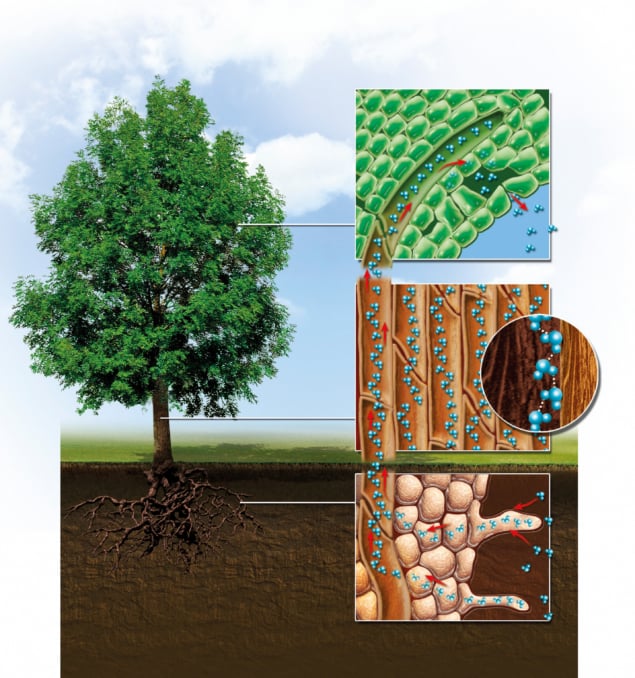
The evaporation sets up a pressure gradient, pulling water up from the roots and through the xylem, as if slurped though a straw. Without transpiration, a tree could get so hot that it might be unable to photosynthesize – indeed, a 2008 study revealed that all trees regulate their temperature so they hover around the 294 K mark (Nature 454 511). However, the process only occurs during the day. After the Sun goes down, the pores in the leaves close, and water molecules left inside the botanical elevator stay in place by sticking to each other and to the dead xylem.
But what makes transpiration so alluring to physicists and engineers is that it’s a “passive” fluid-transportation system. The fact that plants and trees don’t have an “active” pump to ferry water around could help us find novel ways to cool materials in high heat, where space is at a premium. Physicists and engineers have therefore been trying to mimic transpiration for decades, chasing a way to move liquids through a solid to keep it cool. Indeed, transpiration has become particularly interesting to researchers wanting to develop vehicles that can travel faster than the speed of sound. Could trees, therefore, help us to travel at “hypersonic” speeds?
Hot speed
The age of supersonic vehicles began, at least in the public eye, on 14 October 1947, when US pilot Chuck Yeager flew a bullet-shaped Bell X-1 rocket plane faster than the speed of sound. The plane was dropped at altitude from a B-29 and, after burning through its limited fuel supplies long enough to create a shock wave, it glided down to the surface before landing safely. Since then, the world record for the fastest aircraft has soared to many times the speed of sound. The Russian Soyuz capsules or NASA’s space shuttles, for example, plunge through the Earth’s atmosphere at more than 20 times the speed of sound.
“There’s always been a passion to fly faster,” says Kyle Hanquist, a postdoc at the University of Michigan, in Ann Arbor, who is trying to find ways to cool “hypersonic” vehicles – those travelling at or above five times the speed of sound. That need for speed has brought an intense focus on “aerodynamic heat”, generated from friction between the plane’s body and the air, and also from air being compressed directly in front of the craft. For a passenger jet flying slower than the speed of sound, aerodynamic heat plays a minimal role. But at around twice the speed of sound, the aerodynamic heat flux starts to rise exponentially with speed. At high enough speeds, the amount of kinetic energy converted into heat would be high enough to incinerate the plane.
In their quest to build planes and spacecraft that can travel at such speeds, physicists and aerodynamic engineers have been searching for novel cooling systems. Space capsules plunging into the atmosphere, for example, use an “ablative” heat shield at the leading edge, made from resin mixed into fibreglass. The shield is designed to melt and vaporize during descent, creating a thin protective layer as it peels away. By the time the material has vanished, the capsule has slowed enough that it won’t disintegrate.
This approach is fine for one-time uses, but what if you want to have a reusable vehicle and don’t want to waste money repainting it each time? Right now, hypersonic vehicles are built from ultrahigh-temperature composites that are engineered to withstand high heat. Based on metal alloys, these materials can withstand temperatures of around 2000 K, says Hanquist. But as vehicles get faster, they’ll encounter even higher temperatures that would melt or even vaporize these materials unless there are more cooling systems in place.
As vehicles get faster, they’ll encounter temperatures that would melt or even vaporize them unless there are more cooling systems in place
Kyle Hanquist
“We need a different method if we’re going to continue to fly faster,” admits Hanquist, who has been working in his lab in Michigan on cooling hypersonic vehicles by ejecting streams of electrons. But could tree-inspired transpiration be the answer instead? Over the last few decades, physicists have investigated a number of cooling methods that take their cues from plants. They can be found in some “scramjet” engines, for example, which compress incoming supersonic air so that it heats before it burns, making the combustion extra powerful. Such engines, which are the driving force behind many hypersonic vehicles, work most efficiently when boosting craft that are already travelling well above the speed of sound.
To mitigate against the high temperatures that those high speeds bring, some scramjets use transpiration systems that pump a coolant – usually a material with a high specific heat, like water, or gas or even the fuel itself – through the engine. But cooling an engine in this kind of extreme environment with a pump requires space and energy. So to really reap the benefits of biological engineering, physicists need to design a passive system that can cool effectively, but without pumps.
Look, no pumps
A step forward in this pursuit was announced recently by researchers led by Pei-Xue Jiang from Tsinghua University in Beijing, China. Writing in the journal Bioinspiration and Biomimetics (12 056002) from IOP Publishing, which publishes Physics World, they introduced just such a transpiration cooling system. It’s passive, which means it doesn’t use pumps, and it’s self-adaptive, which means it can adjust as the heat flux changes on the surface.
It mimics transpiration using an approach called “porous cooling”, in which a coolant flows through microchannels in a layer of porous material en route to the exterior. The system cools in two ways. First, it absorbs heat from the porous layer as it passes through. Second, when the coolant diffuses to the exterior, it forms a vapour film that protects the outer surface. This approach offers a lot of control over the temperature of the outermost surface.
The structure of the new device is remarkably tree-like (figure 2). It’s also quite small, so maybe it’s more accurate to call it plant-like. It comprises a water tank about the size of a can of soup at the base (like roots), from which rises a flexible plastic pipe. The water travels through the pipe and into a filter that is 30 mm deep. The filter is a porous material made of sintered brass balls, each with a diameter of about 500 µm. The balls themselves are covered in tiny, stomata-like pores, about 200 µm across, that allow the water to evaporate.
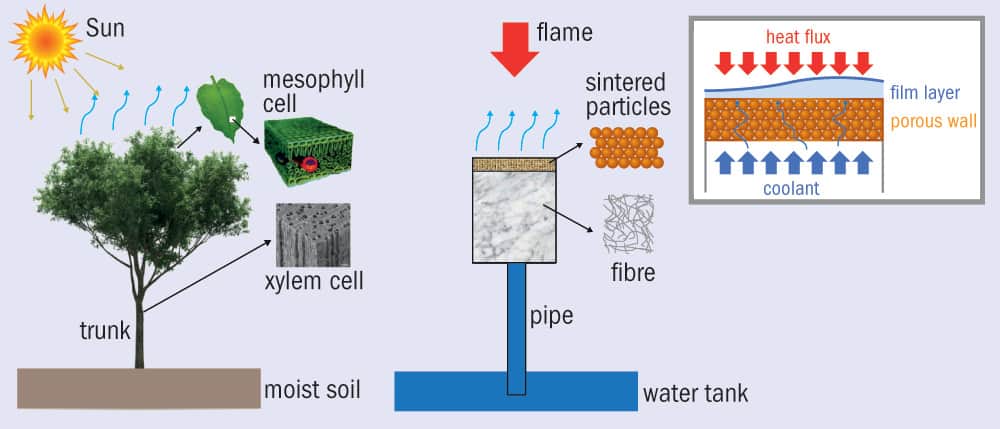
As water evaporates from the surface, it creates a capillary pressure that pulls in more water from the tank, lying 8 cm below. In addition, the evaporating water creates a thin vapour film that protects the surface from the heat. According to the researchers, the system is so effective that when they blasted the surface with a butane flame at 1639 K, it remained a comparably cool 373 K. As they increased the heat flux, the surface remained steady at around 373 K, showing that the system adapted to higher heat to maintain a steady temperature.
Existing transpiration systems that have been used in planes rely on pumps to control the coolant flow, but they take up valuable space and are subject to error. “The pumps significantly add to the weight, which increases the launch costs,” the researchers note in the paper. But a self-adjusting system won’t need additional devices and is closer to an ideal system for hypersonic vehicles – self-adapting and built-in. These jets fly at different altitudes and at a range of speeds, which introduce them to heat flux regimes of varying extremes.
Although lab experiments with this pumpless transpiration system tested a water column only 8 cm tall, the researchers think it could be scaled up – and even suggest how such a system might be used to cool the surface of hypersonic aircraft. “It’s very promising,” says Hanquist. The device might be useful on a smaller scale, as well. In the paper, the researchers also suggest transpiration cooling might be incorporated into heat-resistant gloves that would allow steel workers, boiler operators and others to handle materials above 1000 K. Transpiration in such a glove, note the authors, “is similar to the sweating of an animal skin”.
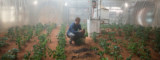
Rocket for rocketeers
From the tallest redwood to the fastest aircraft, the research shows the value of a focus that extends beyond physics. If trees can inspire novel solutions to tomorrow’s high heat problems, then maybe scientists should look to evolved natural systems – and even other disciplines – for solutions to other problems. The learning curve is valuable, but steep. “A lot of people who understand hypersonic vehicles may not also understand biology and trees,” says Hanquist. It’s a case of some people not seeing the wood or the trees.