Abatement techniques can help make industrial processes "greener" by managing gas emissions, as Andy Extance explains
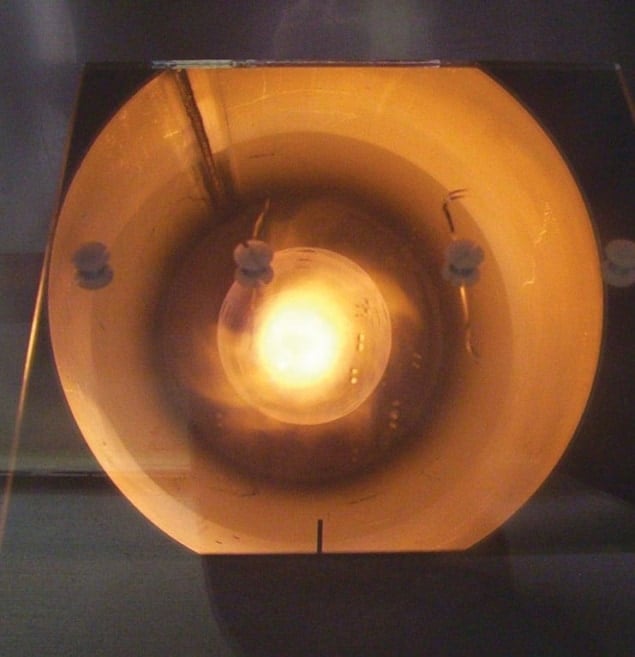
It is not only energy companies that have to pay attention to their greenhouse-gas output. Next year California is scheduled to complete emission rules under its landmark global-warming law, which will set state-wide emissions limits that require the largest industrial sources to report and verify their greenhouse-gas emissions. With voluntary reduction bills being enacted elsewhere in the world, the chances are that many companies will be directly affected by such measures, especially firms emitting the worst kind of greenhouse gases – known as perfluorinated compounds (PFCs).
The semiconductor industry has long used PFCs to clean chemical vapour deposition (CVD) equipment. Between runs that deposit thin layers of semiconductor material onto substrates, nitrogen trifluoride, carbon tetrafluoride or hexafluoroethane are used to remove contaminants from the sample chamber. “CVD manufacturing requires chamber cleaning between operations to maintain the purity of the deposited layers,” says Phil Chandler, global head of environmental products at semiconductor equipment supplier Applied Materials. “CVD is typically the highest priority abatement application for our users.”
From its California headquarters, Applied Materials supplies semiconductor equipment, including both CVD and gas-abatement systems. The firm is advocating the use of fluorine radicals instead of PFCs in chamber cleaning to eliminate the emissions of these dangerous gases. That approach uses microwave heating to create a plasma from PFCs entering the chamber, dissociating them to create fluorine radicals. The fluorine radicals then clean the chamber, forming non-global-warming gases.
Mike Czerniak, product marketing manager at the vacuum pump and exhaust-management company Edwards, warns that even though technology exists to stop such dangerous PFCs being emitted, there is still more work to be done to control their emission. “Carbon tetrafluoride and sulphur hexafluoride are the real heavyweights,” says Czerniak. “Sulphur hexafluoride has 23 900 times the global-warming potential of carbon dioxide.” At Edwards’ site in Clevedon, UK, where Czerniak is based, the main products made to reduce PFCs are combustors, which do a similar job to plasma-based abatement. However, rather than breaking down PFCs as they enter manufacturing equipment, the combustors break down PFCs in the exhaust gases at the end of the process.
Despite incoming regulations by governments across the globe, Czerniak says that firms have not completely resolved their PFC issues. Whereas CVD tools assemble layers of semiconductor material, PFCs are also used to etch the resulting wafers as they are processed to form final devices. Etching uses just 10% of the amount of gas needed to clean CVD tools, but because it uses carbon tetrafluoride, its emissions are more of a problem than many companies realize. “Although less volume is used, the gases are generally more damaging from a global-warming perspective,” Czerniak says. “Etch processing represents the next significant PFC-reduction target,” Chandler agrees. “Today, etch-manufacturing abatement typically concentrates on toxic and corrosion protection, with less attention paid to the destruction of PFC greenhouse-gas species.”
In the semiconductor industry, systems typically handle gas flows of hundreds of litres per minute, of which PFCs may comprise around 10% and the remainder being nitrogen gas. However, these volumes are modest compared with other manufacturing sectors, such as the liquid-crystal flat-panel display and photovoltaic industries. Here they use gas flows of thousands of litres per minute containing a similar proportion of PFCs for tool cleaning. Governments, under pressure themselves to set and adhere to tough emission standards, are keen to control the global-warming potential of such industries.
“We are seeing increasing numbers of manufacturers of flat panels and solar cells appearing in Asia and in particular in China,” says Czerniak. “Manufacturers there are going to have to meet strict local regulations meaning that they must take a more professional approach to handling their waste gases.”
To help reduce processing emissions even further, firms are also targeting their energy consumption. Abatement systems and vacuum pumps have included energy-saving features for some years, but by bringing them together in a single system Edwards claims that it can further reduce the cost of the methane fuel and electricity used. Similarly, Applied Materials emphasizes that its tools raise processing capacity without increasing energy consumption, leading to an effective reduction in emissions.
Today, the world’s electronic-device manufacturers are being joined by other industries directly exploiting semiconductors to help reduce greenhouse-gas emissions, such as the photovoltaic companies and light-emitting-diode producers. Both Czerniak and Chandler underline that to ensure their environmental credentials are clean, these firms must also exploit gas abatement, marking the start of a greater worldwide awareness of emissions.