Nearly seven years after a powerful tsunami caused catastrophic damage to Japan’s Fukushima Daiichi nuclear-power plant, the clean-up and recovery is still ongoing. Bruce Drinkwater and Rob Malkin recently visited the disaster site and the undamaged Tsuruga plant to see if they can pinpoint the true extent of the damage in the dangerously radioactive reactors
The journey to the Fukushima Daiichi nuclear-power plant is a truly sobering experience. When we visited the infamous site in September 2017 our scientific curiosity was dampened by the deserted villages we passed along the way. It was clear from the belongings left behind that the inhabitants had moved out in a hurry following the disastrous earthquake, tsunami and nuclear accident that took place in March 2011. Around 470,000 people had to be evacuated from this region, 154,000 of whom had to leave because of the damaged power plant. With vegetation covering houses and cars, nature has now taken over these abandoned settlements.
These villages are being slowly decontaminated – with some even declared safe – and roadside solar-powered radiation dosimeters have been installed to give the public confidence that things are on track. But despite this, we got the sense that official information remains mistrusted. Combined with the fear of radiation and a lack of jobs, past residents are reluctant to return and the villages they once lived in remain deserted.
We watched these empty houses pass by from a bus operated by TEPCO (the Tokyo Electrical and Power Company, which runs the reactors) as we were driven the 8.5 km from the security checkpoint to the Fukushima Daiichi plant itself. Upon entering the site, we passed large tanks of contaminated water and vast treatment plants designed to remove the radionuclides from the water that is used to cool the remains of the reactor cores. There were numerous large diggers and trucks, many so contaminated that they have themselves become radioactive waste. Then, as we descended a small hill overlooking units 1–4 of the plant, we saw for ourselves the destruction and large-scale construction work being carried out.
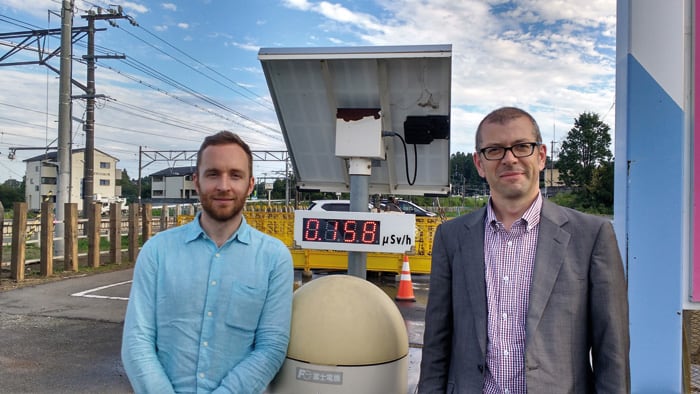
Disaster zone
It is worth recalling the cause of this disaster. On the afternoon of 11 March 2011, a massive 9.1 magnitude earthquake occurred roughly 70 km off the east coast of Japan. The fourth most powerful earthquake of modern times, it created a giant 15 m tsunami that hit the Fukushima Daiichi plant about an hour later. While the plant’s four reactors are 12 m above sea level, the emergency diesel generators that supply back-up power to the cooling systems are only 5 m above the water line. At this lower level, the power of the tsunami was more apparent – large storage drums were distorted by the impact of immense waves, and the emergency power supply and cooling systems of three reactor units were disabled.
Units 1 and 3 subsequently suffered meltdowns, and powerful hydrogen explosions caused extensive damage to the 1 m-thick reactor building walls. Unit 2 also suffered a meltdown but avoided a hydrogen explosion. As for unit 4, which was undergoing maintenance at the time, a hydrogen explosion was caused by gas flowing from unit 3 into the unit 4 reactor.
While the decommissioning process will involve many stages, the first – a comparatively easy task – involves removing used fuel from the spent fuel pools located towards the tops of the reactor buildings. This was completed at unit 4 in 2014. The next task is to remove melted fuel debris, but this can only happen once its location and condition is firmly established.
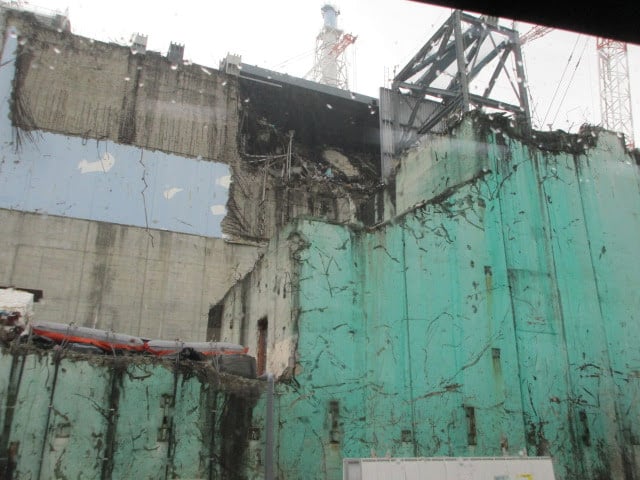
This is why we were in Japan. Our trip was part of a UK–Japan project to create new technology for exploring the hostile environment within the damaged reactors. Our part in this effort is to design new radiation-resistant ultrasonic imaging systems that will help provide more detailed information on the reactors’ current conditions, and allow the long and difficult decommissioning process to really begin. The work is being carried out in collaboration with Hiroshige Kikura and colleagues at Tokyo Institute of Technology, who are researching the robotic systems needed to venture into the inner reaches of this challenging and complex environment.
Our TEPCO bus parked between the badly damaged buildings of units 2 and 3, where the radiation levels for our visit peaked at 270 mSv/h (the annual limit in Japan is 50 mSv). Typical radiation exposure varies widely depending on where you live, but in the UK it is 2.7 mSv per year on average (though the average in Cornwall is much higher, at 6.9 mSv per year). Naturally, we were not permitted to leave the vehicle and were advised not to stay long.
To get a view of what a nuclear-power plant is supposed to look like, we also travelled to the north-west coast of Japan for a tour of the Tsuruga plant, which was untouched by the 2011 earthquake and tsunami. Located on a peninsula bordered by tranquil beaches, the region is a picturesque holiday destination and the power plant lies partially hidden by forest-covered rocky terrain surrounding it on three sides. A 1.5 km tunnel took us through this mountainous interior of the peninsula, and we emerged next to the gleaming white-painted reactor buildings of the plant.
This site has two reactors: a pressurized water reactor (PWR) and a boiling water reactor (BWR). PWRs are the most common type of reactor found around the world and use pressurized water as a coolant to extract heat from the nuclear fuel. BWRs are also in widespread use, particularly in Japan, and operate at a lower pressure, which allows the coolant to boil and the resultant steam to drive the electricity generation turbines directly. The PWR is still operational, though like most nuclear reactors in Japan, is currently offline and waiting for politicians to decide about the future of nuclear power in the wake of the earthquake and tsunami. The BWR that we had come to see is in the early stages of decommissioning and, crucially for us, is of a very similar design to Fukushima Daiichi’s reactors.
Inside a reactor’s heart
Gaining access to the BWR was, quite rightly, not a quick procedure. After exchanging business cards and taking lunch with our hosts, the Japanese Atomic Power Company (JAPC), we attended a briefing that left us in some suspense as to exactly what we were going to be allowed to see as it was given mostly in Japanese. A JAPC bus then delivered us to the security and safety check point where we were issued with entry passes, relieved of our shoes and checked in radiation scanners. At this point, we were also given personal dosimeters, which record total radiation exposure and ensure that nuclear-power-plant workers and visitors stay within strict annual dose limits. Next came a new outfit: light blue socks, gloves, hair net, helmet and even thermal underwear, topped with a light blue boiler suit as the outer layer. A second radiation check, some standard-issue blue shoes and, finally, the preparation process was complete. We passed through an airlock and crossed the threshold into the most tightly controlled area on the site – the reactor building itself.
The interior of the building was hospital-like in its cleanliness and the only sound was a low, persistent hum of machinery. We were led along a network of large and deserted concrete corridors that surround the primary containment vessel (PCV) – a concrete and steel structure enclosing the reactor vessel that is designed to contain any radioactive material in an accident. A very ordinary lift (amusingly almost identical to one in our university department) took us to the PCV’s entrance and, with no ceremony at all, we were ushered into the giant inverted-light-bulb-shaped containment vessel.
The height we entered at was level with the bottom of the reactor pressure vessel (RPV) where the control rod mechanisms are located. These rods control the nuclear reaction by absorbing neutrons, and are inserted and withdrawn by electrical drivers from below the pressure vessel. Standing on the metal grating floor, we were immediately struck by the engineering complexity: pipes and valves and all manner of fixtures and fittings clutter the space, with large painted markers of 0°, 90°, 180° and 270° the only way of maintaining a bearing.
A spiral staircase bought us to the concrete basement of the PCV. At Fukushima Daiichi (figure 1), this is where the fuel from the exploded reactors now rests as a lava-like mess known as corium – an unpleasant mixture of radioactive fuel, the remains of various metals and the products of the chemical interaction between the fuel and the concrete. The 10 m thick concrete floor and the metal shell below are the final barriers stopping that radioactive fuel leaking into the environment.
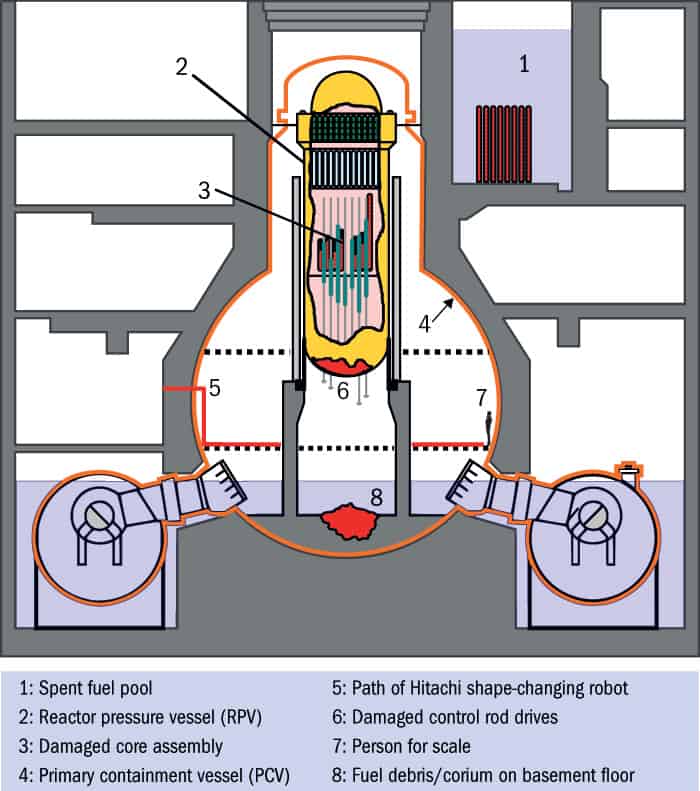
We were now at the bottom of this light-bulb-shaped container where more pipes and other metalwork fill much of the space, providing a rather claustrophobic environment. The RPV itself sits on a 4 m diameter hollow concrete cylinder known as the pedestal, which we could just about see beyond the tangle of pipes. After clambering over large earthquake isolation dampers, there in front of us was a small opening looking into the interior of the pedestal – an uncluttered space compared with the complexity surrounding it. We had arrived at our destination. This is what Fukushima Daiichi’s units 1–3 would have looked like a few seconds before the disaster. And as the pedestal sits directly below the RPV, it is thought that much of the fuel and other debris caused by the meltdown may be contained in this hollow space, although recent images seem to show that some has spewed out of the small openings. After the accident, the PVCs were flooded with water up to a depth of 6 m to cool and moderate the ongoing reactions.
Deploy the robots
To date, a number of shape-changing robots, crawler robots and more recently a submersible robot, have been sent to explore the highly radioactive areas of the Fukushima Daiichi’s reactor buildings. However, access to the pedestal area itself is limited and the extremely high radiation levels near the fuel make it particularly challenging. The crawler robots enter the PCV through a 10 cm diameter tube known cryptically as X-100B. From here they are lowered about 2 m onto the metal grating floor of the PCV’s access level – the equivalent level at which we had entered Tsuruga’s PCV. From videos recorded by the first robots, it was quickly established that this floor has been damaged by heat but is mostly intact apart from a gaping hole through which the molten fuel fell. During the most recent deployment in late 2017, a submersible robot, known as Mambo, was lowered through openings in the metal grating floor, into the water below, to explore the lower regions of the PCV outside the pedestal.
The robots tell us that the radiation dose levels around the metal grating floor are 10–20 Sv/hr. Enough to kill a human in a few minutes, they’re operating in a world in which even specially designed robots and cameras don’t last long because of radiation damage to electronics and cabling. Outside the PCV, radiation levels are high relative to background, but low enough to conclude that the PCV has done its job and contained the fuel. Meanwhile, from the robots’ videos and images, we know that the uranium fuel melted through the bottom of the stricken RPVs and fell into the concrete basement. In some simulated scenarios, the fuel fell in a single large lump, while in others it was sprayed much more widely. However, the true state of the 200 tonnes of uranium is largely unknown, apart from the lower floor images, which show some molten material outside the pedestal.
To survey the location and condition of the fuel, and then help with the eventual removal process, our research group is developing an ultrasonic array imaging technique. Our imaging arrays are made up hundreds of small piezoelectric elements, each acting as an emitter and receiver of ultrasonic waves. In the imaging mode, the arrival times of the return echoes are used to map the 3D scene in front of the device – much like how bats use echolocation to hunt their prey and avoid flying into objects. More elements and larger arrays produce better images, but in the reactors’ space and with the access limitations, the system must be unusually compact – roughly as small as a coffee mug.
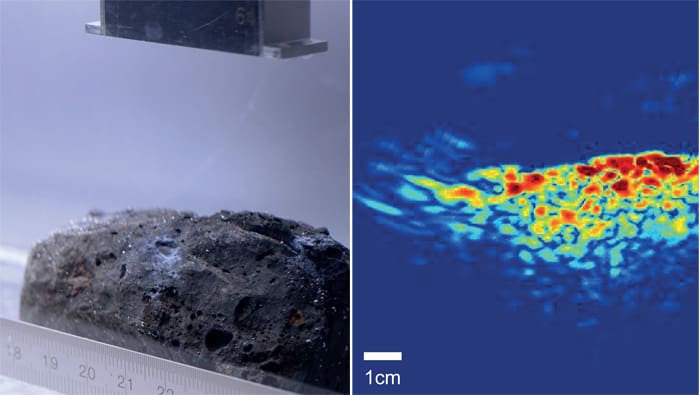
Ultrasonic devices have two major advantages over optical camera systems in this kind of environment. First, the piezoelectric ceramics that they are made from are naturally radiation tolerant, which means that these devices can get much closer to the fuel, for example in the pedestal area, where the radiation levels are expected to be extremely high. Second, they can form images even in water that has been made optically opaque by fine particulates, a problem already encountered by the Mambo submersible robot.
Our imaging system will combine a reasonably standard sonar array for robot navigation and a novel high-frequency array for detailed materials characterization (figure 2). This second system will use the angular reflectivity and frequency spectral features of the ultrasonic echoes to distinguish the various materials that could be present. For example, metallic objects will produce high-amplitude short-duration echoes, whereas porous material such as corium will cause reduced amplitudes and more diffuse scattering. In some cases, it might also be possible to send the ultrasonic waves inside the debris and start to get a picture of its internal structure. Given the current uncertainties, whatever is discovered will be extremely valuable in planning the next steps and allowing decommissioning to begin in earnest.
Fukushima’s future
Our visit to Japan gave us a real sense of what lies lurking in the flooded depths of the damaged Fukushima Daiichi reactors. It is without doubt one of the most challenging environments imaginable. We hope our ultrasonic measurement systems, when mounted on specialist robots, will help form a definitive picture of exactly what state the damaged reactors are in, as only once this picture has become clear can the long process of fuel removal and decommissioning really begin. For us, there is still more research to be done over the next few years, but there is a real prospect that the systems we are developing will be manufactured and sent into the damaged reactors. In some ways, we feel a bit like the scientists and engineers preparing to launch a satellite into space – on the one hand excited, but on the other aware that, once the system is deployed, much of what happens is out of our hands.
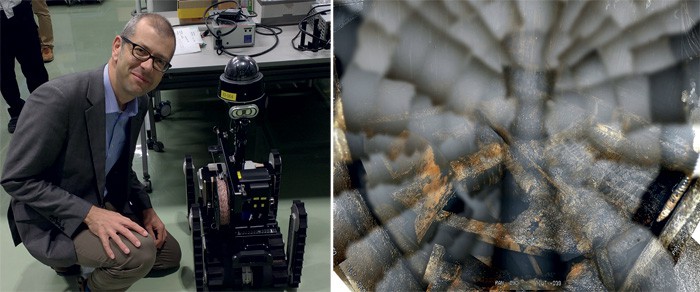
The decommissioning of the Fukushima Daiichi nuclear plant is a multi-faceted science and engineering challenge, in which progress can be made only by scientists and engineers, in academia and industry, working together across national and subject boundaries. So big is the challenge that it will be around for the next 30 years, if not more.
Timeline of a disaster
11 March 2011 Earthquake strikes 70 km off east coast of Japan, causing the emergency shutdown of Fukushima Daiichi and loss of mains power
Fukushima Daiichi is hit by a 15 m tsunami, disabling emergency cooling generators
12 March 2011 Explosion and radiation leak at unit 1
13 March 2011 Sea water injected into units 1 and 3
14 March 2011 Explosion at unit 3
Sea water injected into unit 2
15 March 2011 Explosion at unit 2
Fire and explosion at unit 4
17 March 2011 Helicopters pour water on units 3 and 4
16 December 2011 All reactors are in a state of “cold shutdown”