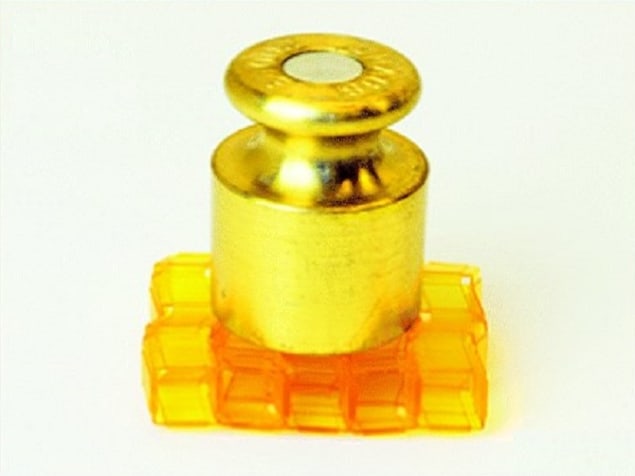
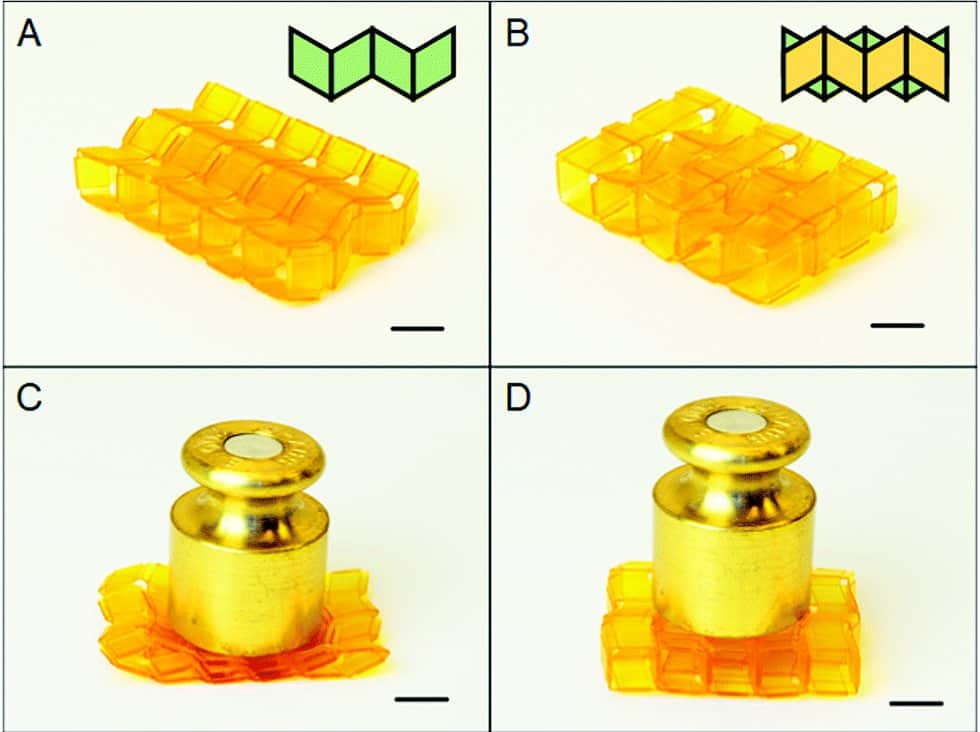
Origami has inspired the design of structures with unique properties, finding a huge range of potential uses, including soft robots and stretchable electronics. Now researchers from Georgia Institute of Technology and Peking University have found a way of directly building reconfigurable origami assemblages using 3D printing technology. The structures can fold and expand, while also having the strength and load-bearing capability required for engineering applications.
Typically, origami structures require the tedious joining together of thin sheets, which can also require additional binding elements. For example, assemblies of multiple paper structures need to be held together with glue. However, with the development of a new polymer and careful geometrical design Zeang Zhao and his team avoid the need to connect smaller parts by devising a way to fabricate a range of 3D assemblies in a single step (Soft Matter). By attempting this, the group are taking the next step towards the implementation of origami for engineering structures.
Origami into engineering
Zhao and his co-workers used a 3D printing technique to fabricate structures comprised of combinations of individual origami units, without the need for any additional assembly step. The analogous paper structure would require sticking together multiple sheets, and a lengthy and tedious step-by-step construction.
The team could design these structures to have different load-bearing capabilities by altering the way the individual origami units are connected. This is crucial for engineering applications. One structure was capable of supporting a load 100 times the weight of the structure itself. However, by simply arranging the same individual units in a different way the researchers built a bridge that will fold flat under the same load.
To construct the origami the group also developed a new “elastomer” – a type of polymer with rubber-like elasticity. By developing this novel material the scientists ensure that the whole structure can be created from a single component. The elastomer could be printed at room temperature and then set using UV light. This formed a soft, foldable material, capable of being stretched up to 100%, which they used for the entire 3D assembly in their structures.

Origami brings soft logic to robotics
Special hinges
The researchers designed the structures to consist of thick panels, separated by hinges that mimic the creases in paper. The thickness of the hinges is crucial to the mechanical properties: too thin and it may not support the whole structure, too thick and it will limit how well it can fold. Their hinges allowed the angle between the panels to vary between 0° and 90°. The team were also able to ensure that the high stress and strain experienced during folding is localized to the hinges. This means the panels do not become deformed with use.
3D printing
While still an emerging technology, 3D printing has proved useful for creating a huge range of complex geometries. However, the traditional method is generally only suitable for producing solid structures. In order to print structures with hollow features, the team used a different 3D printing technique called digital light processing. This requires much less support material, allowing hollow features to be created. It also permits printing of the softer materials, needed for flexible structures.