Kaoru Sato, Haruo Nakamichi and Hitoshi Sueyoshi explain how neutron science and strong industry–academia links support innovation in Japan’s steel industry
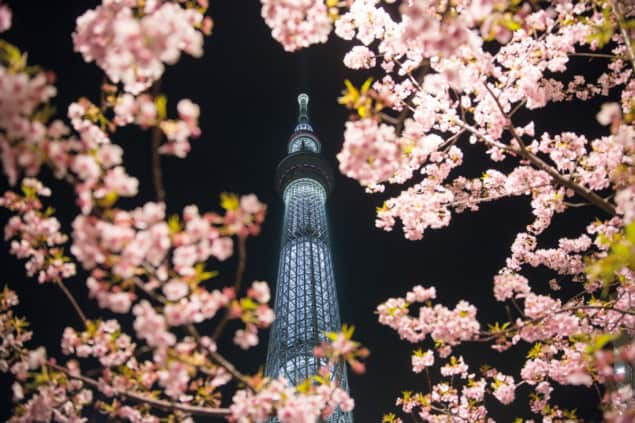
The world produces 1.6 billion tonnes of steel every year. According to analysts at AME Research, this figure could grow to as much as 3 billion tonnes by 2050. For the steel industry, however, improvements in quality matter as much as increases in quantity. The importance of continuous improvement can be seen by comparing the Eiffel Tower with modern steel structures such as the Tokyo Skytree. The former is 324 m tall – a record at the time of its completion in 1889 – and made of wrought iron, a material that begins to deform irreversibly when subjected to stresses of 100–200 MPa (the yield stress). In contrast, the weldable high-strength steel used for the 634 m Tokyo Skytree has a yield stress of up to 630 MPa. Without innovation in steel, such a huge construction would not have been possible.
The steel industry has long been alert to emerging technologies and keen to benefit from them. The Japanese steel firm Nippon Kokan (a predecessor of JFE, our employer) began using state-of-the-art microbeam analytical instruments such as the transmission-electron microscope (TEM) and electron probe micro-analyser (EPMA) as early as the 1960s. TEMs were used to observe microstructures such as dislocations and small precipitates in steel, while the EPMA was mainly used in the steel-making division for measuring elemental segregation and non-metallic inclusions such as oxides and sulphides. More recently, analyses based on synchrotron radiation have also become widely used for R&D in Japan’s steel industry.
History lesson
Compared with X-rays and electrons, neutrons are a less common tool. The relative rarity of neutron beams was, until fairly recently, a high hurdle to their use in the steel industry. Nevertheless, beginning in 2006, JFE began to promote the use of neutron scattering to analyse the microstructures of large-volume steel samples. The history of our approach is documented more fully in a recent report (2017 JFE Technical Report 22 1–5), but the following summary covers a few of the most important points.
One promising technology for developing high-tensile-strength steel involves dispersing tiny particles (mostly carbides such as titanium carbide and niobium carbide, but sometimes metallic copper) within the steel matrix. These nanometre-sized precipitates hinder the movement of dislocations in the matrix, making the steel strong without sacrificing its formability (at least, not too much). Electron microscopy is a powerful method for directly determining the size and distribution of these precipitates, but the area that can be observed with this technique is limited and the statistical procedures for extrapolating to larger (and thus more representative) areas are tedious. It is also not easy to evaluate nanometre-sized precipitates with chemical extraction methods, since such small particles are often chemically unstable and difficult to collect with filtration.
In comparison, we have found that non-destructive neutron measurements possess considerable advantages, combining reliable data from bulk steel with ease of use. In one series of experiments, we used small-angle neutron scattering (SANS) to determine the size of nanometre-sized titanium carbide (TiC) particles within 10 × 10 × 2 mm (thick) sheets of hot-rolled steel. The sample volume for this measurement was about 108 times larger than that used for ordinary TEM thin-foil observations. In the “Particles” figure (a) shows the SANS profile change as a function of heat treatment in this steel. This profile enabled us to determine the average size (b) and the number density of TiC particles. Such knowledge is important because optimizing precipitates is a time-consuming procedure, with numerous combinations of micro-alloying elements and heat treatments that can be tried.
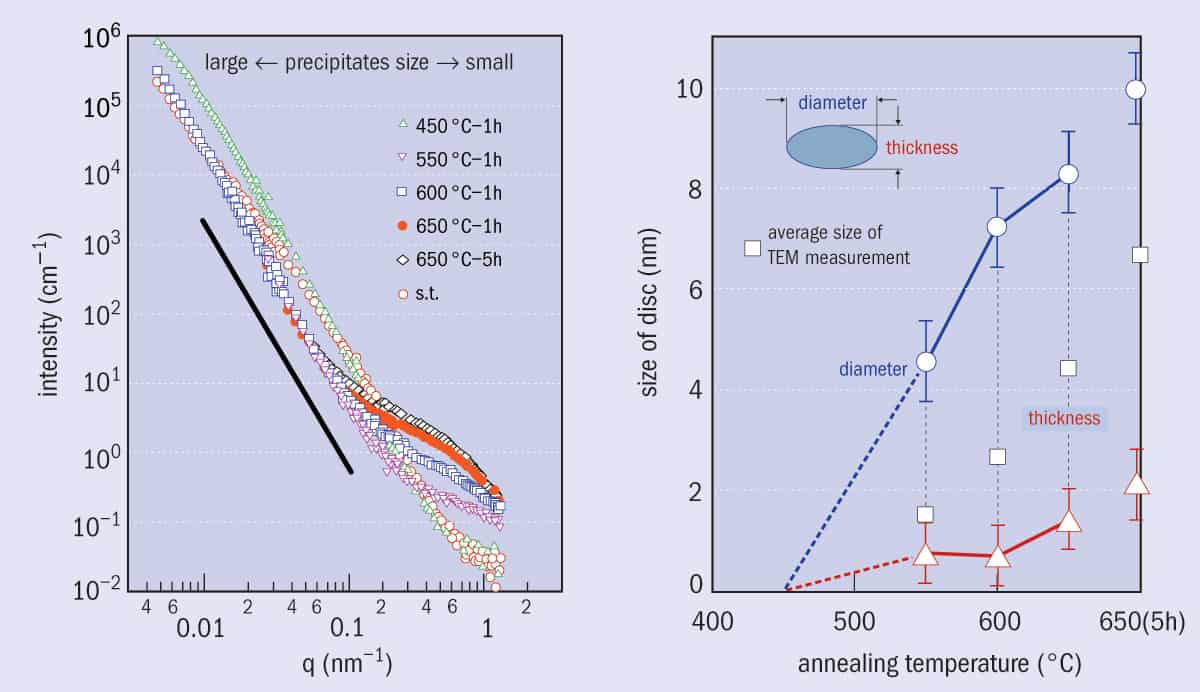
A promising approach
The promising nature of our approach led the Institute of Steel and Iron of Japan (ISIJ) to award its 2011 Tarawa best paper award to JFE Steel and our collaborators at the Japanese National Institute for Materials Science (NIMS), the Japan Atomic Energy Agency and Ibaraki University. The easy and precise evaluation of precipitation from bulk steel, without the need for tedious specimen preparations, will certainly promote R&D of new types of steel.
In addition to studying precipitates with SANS, we are also using neutron diffraction to study steel texture, and to analyse residual stress in welds. The “Welds” figure is an example of a contour plot of (transverse) lattice strain in the weld joint of welded 980 MPa grade steel. At the welding site, there is an increased risk of cracks due to residual stress from the welding and from absorption of hydrogen. Neutron diffraction revealed that the root portion of the weld experiences the highest stress – over 1000 MPa – in the transverse direction. Tensile stress at the root is also present along the weld line and in the plate thickness direction. From this analysis, we were able to infer that high levels of tensile residual stress and the resulting hydrogen accumulation is the key factor for cold cracking. Hence, this neutron-based analysis gave us an important insight into ways of optimizing the weld metal and the welding conditions. As demand for even higher-strength steels continues to increase, the development of steels that are less susceptible to hydrogen embrittlement is vital.
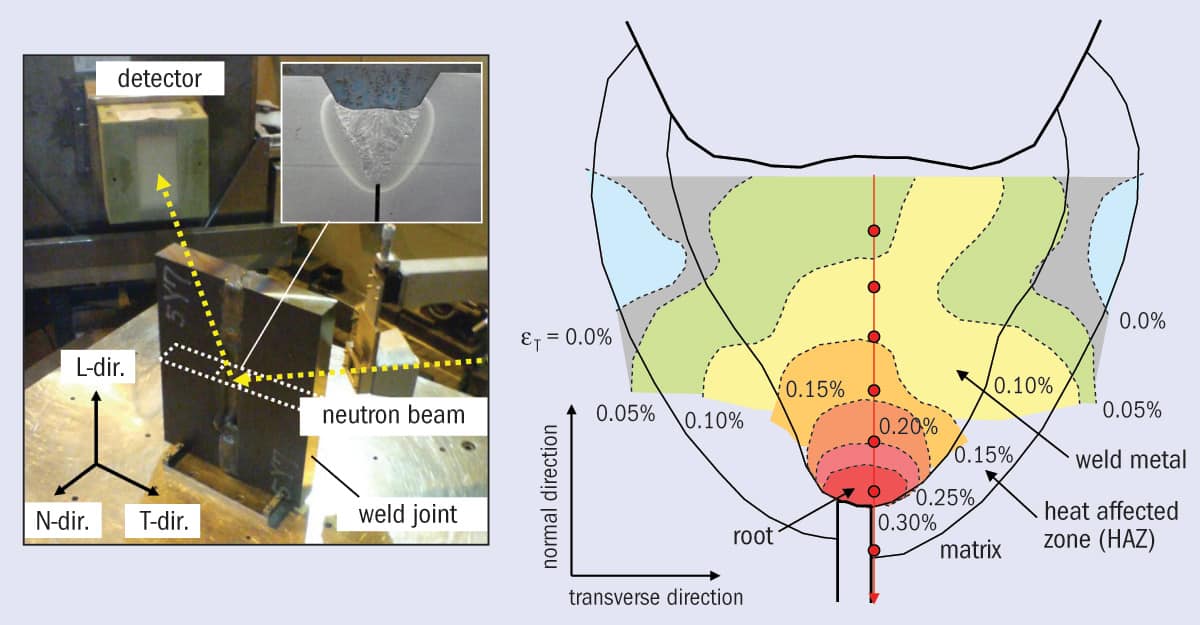
Another application of neutron diffraction concerns “retained” austenite in high-tensile strength steel. Austenite is a high-temperature phase of steel with a face-centred cubic structure, and normally it transforms into ferrite (which has a body-centred cubic structure) when cooled. However, with careful control of the heat treatment, areas of steel with high carbon and/or manganese content can be “retained” in the austenite phase even at low temperatures, including room temperature. This is useful because when steel containing retained austenite is deformed, the austenite is transformed into another phase, martensite, creating a strong, ductile material known as TRIP (transformation-induced plasticity) steel that is widely used in the automotive industry. Neutron diffraction is useful for measuring the fraction of retained austenite in steel by volume – something that electrons and X-rays cannot do, because they cannot penetrate very far below the material’s surface. In the future, we hope to fully exploit the potential of neutrons to improve dynamic measurements of phase transformations, and also to analyse hydrogen in steel and perform 3D imaging of embedded defects or inhomogeneities.
Strong collaborations
As the application of neutrons to steel research is still relatively new, it is worth taking a closer look at how this research started and how it has been promoted in the steel community in Japan. The research described in the previous section would not have been possible without the efforts of Yo Tomota, a materials scientist then at Ibaraki University (now at NIMS), who pioneered the use of neutrons in steel research, and who organized a research group with JFE Steel under the auspices of the ISIJ. In 2006 the ISIJ chose the development of neutron-based techniques for steel research as its first industry-driven collaborative project. Scientists from other major steel companies and from academia – including both materials and characterization experts– joined in. Over a three-year period, members of the group tested various neutron techniques, including reflectometry as well as SANS and neutron diffraction.
Having scientists who are “multilingual” in both industry and academia, is, we believe, the key to a successful synergy
During the second stage of this group’s work, something very unfortunate happened: the To¯hoku earthquake and tsunami devastated Japan, and the Japan Proton Accelerator Research Complex (J-PARC) and many nuclear reactors had to cease operations. This prompted us to think hard about possible alternative neutron sources. For the third stage of the ISIJ neutron research activity, we strengthened our collaboration between ISIJ members and RIKEN, Hokkaido University and Kyoto University (all of which possess compact or medium-sized neutron sources). In recent years, members of the group have been evaluating the feasibility of using compact neutron sources for steel-related research topics.
In July 2017 at the International Conference on Neutron Scattering in Daejeon, Republic of Korea, one of us (KS) gave a presentation outlining JFE’s use of neutrons. Afterwards, an audience member observed that it is not easy to stimulate interest in neutrons from industry scientists, and asked why JFE was an early adopter in this area. The immediate answer was that historically, Japanese companies have strong R&D divisions, and the research scientists who work there (in analysis, for example) are used to collaborating closely with academic scientists as well as with process development and steel product development engineers. This means that scientists working in analysis and characterization can understand the languages of both neutron scientists and materials scientists in the company.
Having scientists who are “multilingual” in both industry and academia, and who can therefore bridge or mediate between each side, is, we believe, the key to a successful synergy. It is worth noting that the steel industry is not the only sector of Japanese manufacturing to place high expectations on neutron technology. RIKEN has provided an excellent summary of the ways neutrons are being used in Japanese industry, as well as the fundamentals of neutron science.
Even so, we believe that further steps are still required for neutrons to become a common measurement tool within industry. Measurements using neutrons are generally easy; however, users often have to wait for several months or even longer for experiments after their proposals are approved. On the other hand, we can use electron microscopes and X-ray diffractometers daily. This lack of accessibility is a huge bottleneck for expanding neutron applications. Recognizing this problem, in 2015 the Japan Science and Technology Agency began an A-STEP (Adaptable and Seamless Technology Transfer Program through Target-Driven R&D), aimed at developing key technologies for compact neutron sources and their industrial applications. This A-STEP includes 10 research themes, and is being supervised by Hideki Yoshizawa of Tokyo University and seven research advisers – including five from industry.
Achieving goals
We hope that laboratory-scale neutron measurements will become routine in the near future. In order to achieve this goal, further collaboration between industry and academia is a must. Demonstrating useful results is the only way to ensure that industry will show more interest in neutrons and even invest in such research programmes.
- Enjoy the rest of the 2017 Physics World Focus on Neutron Science in our digital magazine or via the Physics World app for any iOS or Android smartphone or tablet.