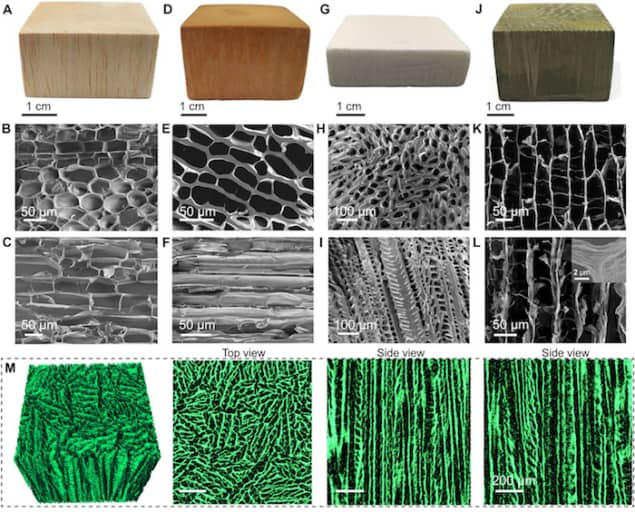
Researchers in China have developed a new way to make life-like artificial wood on a large scale from a polymer called resol, which is very similar to lignin (the compound found in natural wood). The manmade wood is as light and strong as its natural counterpart, but it is also resistant to fire and acid.
Wood is one of the most common natural materials. It has many good properties, such as its light weight and high strength, which comes from its unique hierarchical cellular structure and matrix (made from lignin and hemicellulose) embedded with well-oriented cellulose fibrils. Wood grows (very slowly) in a controlled, bottom-up way and every structural level contributes to its remarkable properties.
In recent years, researchers have succeeded in making “super-woods” by modifying the microstructure of natural wood or combining wood-derived cellulose with synthetic materials. Although these materials are impressive in terms of biodegradability and are tough, they are still inflammable and not very resistant to corrosion by acids. Ceramic-based woods grown up by bottom up techniques (such as freeze-casting or 3D printing) using polymers as the binders and micro- or nano-scale powders as the building blocks also show promise but they are often mechanically weak and their microstructures cannot be easily controlled.
A “chemical web”
Researchers led by Shu-Hong Yu of the University of Science and Technology of China (USTC) are now putting forward a new way to quickly make bulk quantities of synthetic polymeric wood that looks and feels very much like the real thing. To do this, they first dissolved resol in an acid chitosan solution to form a homogenous mixture. They then poured the solution into a mould (for example, an open-ended cylinder) placed on a cold copper platform and frozen in one direction at a constant freezing rate. “We then immersed the copper in a liquid nitrogen bath and after freeze-drying, cured the polymeric cryogel at high temperatures of 180°C,” explains Yu.
“Resol, which is very similar to natural lignin, acts as ‘chemical web’ that holds the cellulose fibrils in the chitosan together,” he adds. “We were thus able to create matrices on which self-directing crystals grow at low temperatures. Different particles, such as metal ions and nanowires/sheets can be incorporated into the polymeric wood at this stage to vary its appearance or physical properties.
“We can control the cellular structure of the new wood (its components, pore size and wall thickness) during fabrication,” Yu tells Physics World. “The wood has many good properties. These include its low density (90-600 mg/cm3) and high compressive strength (of 45 MPa), which is comparable to that of natural wood.”
And that is not all: the polymeric wood is also resistant to acid, in contrast to natural wood, with no decrease in mechanical properties. “It is also boasts a thermal conductivity as low as around 21 mW/m/K, which puts it on the same rank as state-of-the-art thermal insulators, like polymer/SiO2 hybrid composites,” adds Yu. “It is also a good fire retardant and self-extinguishes quickly when removed from the igniting flame – something that is not at all the case for natural wood.”
The researchers say that their new wood might be used as an alternative to natural wood in harsh environments. “Our new strategy to make artificial wood could also be applied to engineer a wide range of high-performance biomimetic engineering composite materials with specific functions that are better than their traditional counterparts,” says Yu. “These materials will find broad applications in a host of technologies.”
The team, reporting its work in Science Advances 10.1126/sciadv.aat7223 is now busy improving the weather resistance of its polymeric wood so that it can be used in practical outdoor applications. “We are also trying to make other classes of artificial woods by using materials other than resol.”
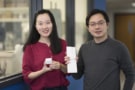
‘Nanowood’ makes a super thermal insulator