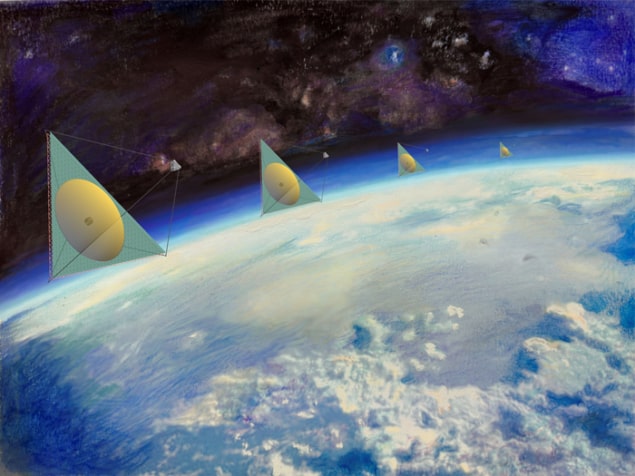
Extremely large telescopes in space- or balloon-based observatories will require mirrors that are much larger, more sensitive and lighter than those in operation today. Large membrane mirrors with low areal weight show promise in this context, but they are difficult to manufacture with the required optical quality.
Researchers in Germany have come up with a new way to make very thin polymer mirrors of a high enough quality to serve as the primary mirrors in space telescopes, using an approach that’s very different from conventional mirror production and polishing processes. The technique, developed by a team at the Max Planck Institute for Extraterrestrial Physics, involves depositing a polymer onto the surface of a rotating liquid that forms a perfect parabolic shape. The resulting mirrors are lightweight, measure around 30 cm in diameter and could potentially be scaled up to much larger diameters of metres. They are also flexible enough to be rolled up for transport on a spacecraft and unfolded once it reaches its destination.
In their work, the researchers, led by Sebastian Rabien, made use of a basic physics phenomenon: that a liquid in a spinning container will naturally form a parabolic surface shape. They used this surface as a base on which to deposit a polymer – Parylene, in this case – with the desired thickness. Once coated with a reflecting surface such as aluminium or gold, this membrane can be used as a mirror.
The polymer is grown using chemical vapour deposition. This technique is routinely employed to apply coatings on electronics, but this is the first time that it has been used to create parabolic membrane mirrors. “The entire process takes place in vacuum, free from disturbing winds or particles, which allows for optical quality surfaces,” explains Rabien.
The researchers say that they can locally manipulate the parabolic shape of the mirror using a radiative adaptive optics method, which involves thermally expanding the material by applying a light beam to the front or back surface of the structure.
The new mirrors could be rolled up and stored compactly inside a launch vehicle, and then unfolded and precisely reshaped after deployment – something that helps to solve weight and packaging issues for telescope mirrors, says Rabien.
“While surely more research and engineering is needed, I think that we have a process that is scalable to very large diameters (15–20 m),” he tells Physics World. “The liquid mandrel for the surface shape is also significantly more affordable than conventional optics production methods. Vacuum chambers of the size needed to make these mirrors already exist for other purposes and the growth processes required can be adapted from available technologies.”
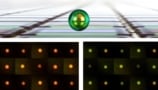
Nanoparticle-on-mirror constructs could help make colour-changing displays
One type of astrophysical object that could be imaged and searched for using such mirrors is exoplanets, says Rabien. “The vision of looking at those distant planetary systems at high resolution and sensitivity, resolving weather or continents, or even lights on a coastline, would require many large telescopes with such mirrors to be placed in orbit. Making this dream possible does need a significant reduction in areal weight and cost of the primary mirror, and a way to pack those into a launch vehicle. The techniques described in our work could be a pathway towards such a vision.”
The researchers, who report their work in Applied Optics, say they would now like to use their technique to make mirrors metres in size. “This would allow us to better understand the surface function of the mirrors and how to influence and control it, and quantify the large-scale control parameters required.”