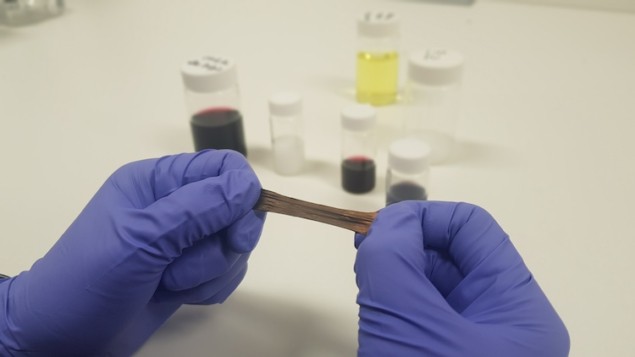
Stretchable conductors that stay conducting even when stretched by as much as 300% in any direction could find use in a new generation of deformable and wearable electronic devices. The conductors are made by sequential layering of polymers and gold nanoparticles in a design that is the first of its kind according to the researchers who developed them.
Stretchable electronics are in demand for a number of applications, such as wearable healthcare devices, electronic skin, artificial muscles and neuroprosthetic implants. All these applications ideally require stretchable conductors that have high electrical conductivity under large mechanical strain, but such materials are difficult to make.
Layered composite film sheets
There are two main strategies to make such conductors. The first involves depositing conductive nanoscale components onto the surface of an elastomeric substrate to reduce conductivity loss when the material is deformed. These composites unfortunately only contain a small amount of conductor though. In the second, researchers disperse conductive fillers in elastomeric polymers. Although these composites carry a high current and can self-heal, they are either prone to fail at low strains if they contain a large amount of stiff conducting material or have low intrinsic conductivity if they contain a high amount of elastomer.
A team of researchers led by Nicholas Kotov of the University of Michigan in the US, Soojin Park of POSTECH in Korea and Byeong-Su Kim of Yonsei University in Seoul, Korea, has now developed stretchable conductors using a new type of film made from multiple layers of positively charged gradient-assembled polyurethane (GAP) and negatively charged gold nanoparticles. The layered composite film sheets contain different ratios of gold nanoparticles, weighted at 90% at the top and bottom outermost surfaces and either 50 or 85 weight percent film to create a stretchable layer in between.
“This sequential layering of the polymers and nanoparticles in a specific sequence can be optimized for both mechanical and electrical properties,” explains Kotov, “and the stratified design is key to attaining tunable conductivity and stiffness.” Indeed, it allows the researchers to structurally organize the material on both the small and large scales, which means that they can align and interconnect the gold nanoparticles even under large strains so that they remain highly conducting.
“This approach to materials engineering is in fact typical for the design of many biomaterials and allows for wide range tuning of both mechanics and electrical transport,” he tells Physics World.
Strain can be applied along any direction
Importantly, the strain can be applied along any direction in the material, which retains its metallic conductivity in both the lateral and transversal directions even at strains of as high as 300%, he adds.
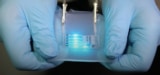
Printed metal-polymer conductors make stretchy biodevices
To test their material, the researchers used it as the electrode in a lithium-ion battery. They measured a charge-discharge rate capacity of 100 mAh/g at a current density of 0.5 A/g in this device, which continues to work at 90% of its original capacity even after 1000 battery cycles.
The result could allow for the development of stretchable lithium-ion batteries that deliver stable power even when deformed, they say.
“These materials and stretchable devices made from them open the road to a new generation of implantable biomedical devices with integrated batteries that are able to deform in a variety of directions inside the body,” explains Kotov. “They could thus be employed in constrained environments inside organs, for example, and perhaps even in the vicinity of neurons.”
They might also be used in soft robotics applications, he adds.
The stretchy multilayer conductor is described in Science Advances 10.1126/sciadv.aaw1879.