Scientists from the University of California at Berkeley, US, and Lawrence Berkeley National Laboratory, US, claim they have made the first true NEMS (nanometre-scale electromechanical system) device based on a multiwalled carbon nanotube. At the heart of the synthetic actuator is a rotating rectangular metal plate attached to a nanotube support shaft (A Fennimore et al. 2003 Nature 424 408).
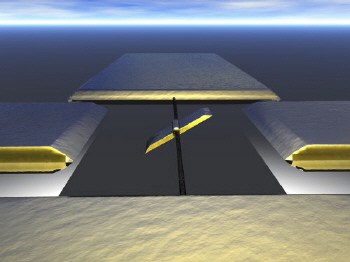
“Without question the potential of NEMS actuators/motors is huge – only the timescale for this to be realized is an unknown,” Alex Zettl of the University of California at Berkeley told Nanotechweb.org “Many of my MEMS – microelectromechanical systems- colleagues are chomping at the bit to incorporate such nanoscale bearings, motors and actuators into higher order NEMS/MEMS systems. Apparently they just don’t have good low-friction, high-Q materials that operate effectively at this size scale.”
The Berkeley device’s components are integrated on a silicon chip. The nanotube support shaft for the rotor plate spans the gap between two electrically conducting anchors. The rotor plate assembly is also surrounded by three fixed stator electrodes – one to each side and one buried beneath the substrate surface. By applying a voltage of up to 5 volts to the rotor plate and stators, the scientists were able to control the position, speed and direction of rotation of the rotor plate.
The nanotube both acts as the support shaft and provides an electrical connection to the rotor plate. To bring low-friction properties to the nanotube shaft and to enable the rotor plate to rotate through a full 360°, the team sheared away the outer nanotube shells by applying very large stator voltages – around 80 volts.
“Our synthetic devices have many advantages over the molecular motors already known in biology,” said Zettl. “Nature has been exceedingly clever in designing various kinds of molecular (i.e. nanoscale) linear and rotational motors – such as kinesin, ATP synthase, flagellar motors of bacteria – but these are pretty darn specific. They cannot survive over a very wide temperature range, need aqueous environments with tightly controlled chemical balance, and are actually quite slow – they cannot exceed kHz.”
In contrast, Zettl says there is no reason why the synthetic actuators/motors should not operate from cryogenic temperatures up to at least hundreds of degrees C, in environments from vacuum to fluids, and from dc to even microwave frequencies. “While our synthetic motors will not compete with biomotors in certain applications, they most certainly break the applications field wide open, to arenas where nature’s existing motors simply were not meant to, and cannot, survive,” he said.
The rotor plate could act as a moveable mirror for optical switches, for example, or as a paddle for fluid manipulations. “While many of these applications will revolve around communications and mechanical sensor systems, there is an equally large potential in the chemical/biological arena, including microfluidics, chemical sensing and nanotube-bio-motor hybrids,” continued Zettl. “Just like projections made in the early days of lasers, integrated circuits and MEMS, I think no matter how broad and visionary we try to be, we will greatly underestimate the impact – and no doubt also misjudge where the most successful applications will be.”
Now the team is pursuing “chemically and biologically inspired extensions of this work” as well as developing aligned arrays of nanoactuators/motors, and incorporating them into higher order structures with sophisticated functionality.