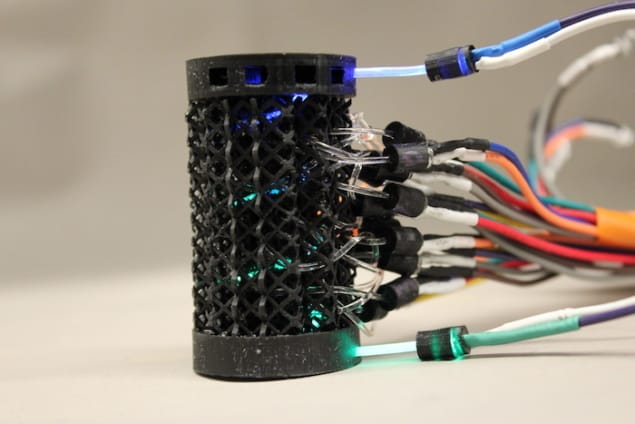
A new sensor containing optical fibres embedded in a 3D-printed elastomer could make for a sensor network that allows robots to feel touch and sense how they interact with their environment. The optical lace, as it has been dubbed, could be distributed throughout the body of a robot and is similar to a biological nervous system as well as being stretchable. It can localize applied deformations with sub-millimetre positional accuracy and sub-Newton force resolution (0.3 N).
In the biological world, animals with poor vision have evolved other forms of perception, such as touch, to navigate their environment thanks to complex networks of nerves distributed throughout their bodies. Although researchers have succeeded in making artificial skin with tactile sensing for robots, wiring nerve-like networks throughout the body of a robot has proved more difficult.
A team of mechanical engineers led by Patricia Xu and Rob Shepherd of Cornell University in the US has now made an optical lace comprising optical fibres that host more than a dozen mechanosensors embedded in a 3D-printed elastomer (polyurethane) attached to a light-emitting diode that could overcome this problem.
Optical guides detect level of deformation
When the lattice structure is pressed, the optical guides detect the level of deformation (buckling and bending) experienced by the struts in the 3D lattice by measuring the intensity and location of light loss in the optical fibres through coupling. The intensity of the coupled light determines the intensity of the deformation itself, explains Xu.
The researchers say that the optical lace can be distributed throughout the body of the robot and not just coated on its surface. It allows the robot to be both exteroceptive – that is, sensitive to touch, so that it can detect where it is pressed – and proprioceptive so that it can measure the level of its own compression and “be aware” of its own body.
The optical lace is similar to a biological nervous system in which individual mechanoreceptors are embedded in the skin and muscle at different locations, explains Xu.
“In animals, these sensors send information about the size and location of deformation to the brain for processing. In the same way, our optical lace has distributed sensors throughout the structure that report the magnitude and position of deformations to a computer. The location is encoded in the position of the sensor and the intensity of light coupled encodes the magnitude of deformation.”
Safer interactions with people
Our optical sensors are more stable compared to many other stretchable electronic sensors, she tells Physics World. “In robots, if the sensor is placed closer to the surface in the right orientation, we can measure externally caused deformation (exteroception) and if it is placed deep inside the structure, it measures internal deformation (proprioception).”
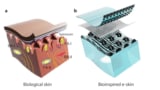
Bioinspired e-skin could help domestic robots sense touch
Integrating these sensor networks into robots could allow them to more safely interact with people, adds Shepherd. “We are hopeful that, eventually, systems like these will allow robots to assist the elderly and people with reduced abilities. In such applications, the robot would need to know its own shape in order to hold and assist a person without hurting them.”
“Softer than cold, hard cyborgs”
Such robots, which would be softer than the cold, hard cyborgs we are used to seeing in science fiction films, could also be used in manufacturing, he adds. “If they can feel what they’re touching, then that will improve their accuracy.”
In their work, which is detailed in Science Robotics 10.1126/scirobotics.aaw6304 and supported by the Air Force Office of Scientific Research and the Office of Naval Research, the researchers employed physical models to translate sensor signals into deformation states. “In the future we would like to make larger networks and produce more complex deformations, so our current physical models will not work as well,” says Xu. “Machine learning could come in useful here to create these more sophisticated models and detect distortions, like bending and twisting.”