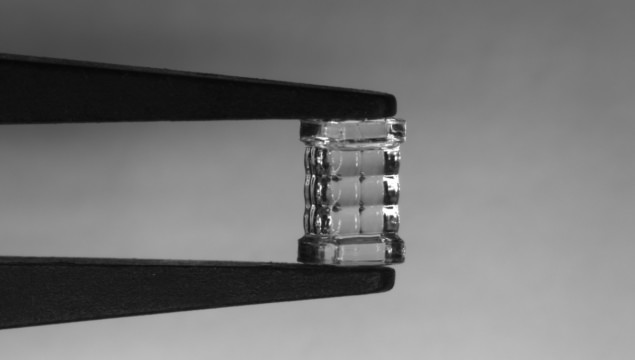
Additive manufacturing, also known as 3D printing, has revolutionized many sectors with its speed, flexibility and unparalleled design freedom. But previous attempts to create high-quality optical components using additive manufacturing methods often came up against a range of obstacles. Now, researchers from the National Research Council of Canada have turned to blurred tomography – an extension of the tomographic volumetric additive manufacturing (VAM) method – to create customized optical components.
“3D printing is transforming every sector of manufacturing,” says lead author Daniel Webber. “I’ve always been interested in 3D printed optics due to their potential to revolutionize optical system design. I saw a post-doc position with the NRC where they wanted to do volumetric 3D printing of micro-optics, and the rest was history”.
Additive manufacturing challenges
In the past, techniques such as digital light processing, stereolithography, inkjet printing and two-photon polymerization (2PP) have been used to build optical components through a layer-by-layer approach. However, the fabrication process tends to be slow, it’s difficult to fabricate optical components with curvature – which many components need – and surfaces that aren’t parallel to the substrate have height steps defined by the layer thickness.
VAM has also had its challenges, with poor part quality (such as ridges on the surface called striations) due to the self-writing waveguide effect – in which the narrow writing beams used in VAM cause increased printing speed in planes parallel to the beams. Post-processing methods are usually required to increase the part quality and smooth the surfaces, but a direct VAM method that doesn’t require extra steps has been sought.
Overcoming challenges with blurred tomography
In their latest research, Webber and his team have accomplished such a direct VAM method, while maintaining the freedom of design that additive manufacturing offers for rapid prototyping.
Tomographic VAM uses projected light to solidify a photosensitive resin in specific regions, enabling parts to be built without support structures. While the pencil-like beams used in conventional tomographic VAM methods cause striations, the new technique can produce microlenses with commercial-grade quality. It is known as blurred tomography, because a large-etendue (more “spread out”) source is used to purposely blur the lines and reduce striations.
The blurring of the optical writing beam helped to generate a surface roughness in the sub-nanometre range – making it essentially molecularly smooth. By comparison, other VAM methods have well-collimated and low-etendue writing beams so that they are not blurred by design.
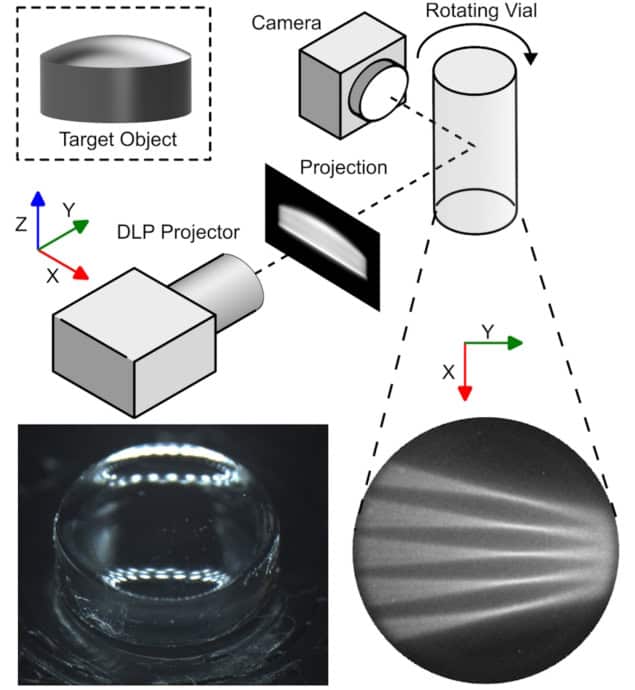
By purposely blurring the beam and coupling it with astigmatism introduced by the cylindrical vial of photoresin (without an index matching bath), the blurring could be achieved across the whole print volume. Alongside the rapid processing speed, the other defining feature of the blurred tomography method is that it doesn’t require additional processing and is therefore a direct method for producing smooth optical components.
“The most significant finding of this work is that we can directly fabricate optically smooth surfaces and have freeform ready-to-use optical components in under 30 minutes,” says Webber.
While the overall processing time takes around 30 min, the actual printing of the lenses took less than a minute. This is similar to other VAM techniques (but without the need for extra surface processing steps). In comparison, a previous study found that using 2PP to print a half-ball lens of similar size (2 versus 3 mm), curvature error (3.9% versus 5.4%) and surface roughness (2.9 versus 0.53 nm) took 23 h – showing how blurred tomography is much faster, while producing finer surface features.
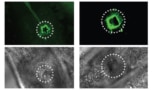
Laser-printed electronics could create next-generation medical implants
The research team showcased the potential of the new technique by making a millimetre-sized plano-convex optical lens with an imaging performance comparable to that of a commercial glass lens. The intrinsic freedom design that additive manufacturing offers also helped the researchers create a biconvex microlens array (fabrication on both sides), as well as overprinting of a lens onto an optical fibre.
Like many areas of additive manufacturing, it’s thought that VAM could offer a way of producing low-cost and rapidly prototyped parts, in particular, freeform optical components. “We have demonstrated that blurred tomography is capable of rapidly fabricating a range of micro-optical components. Moving forward, we would like to extend these capabilities to larger part sizes and new materials,” Webber tells Physics World.
The research was published in Optica.